What is surface preparation
Surface preparation is defined as “the cleaning or preparing of the metal surface prior to the application of a coating.” In practice, surface preparation embraces many things, which fall under this term. For example, the removal of mill scale , rust, removal of imperfections, removal of existing coatings and or other contaminants. The creation of a profile on the metal surface also falls under the preparation of surfaces. In this way a good adhesion layer is created between the object and the coating that is applied to it.
It can be performed by using chemicals to clean and treat the surface, or by using mechanical methods to alter its texture or remove unwanted substances such as weld spatters. To prepare materials like (stainless) steel, aluminium and wood, different surface preparation techniques can be used.
The importance of surface preparation
Surface preparation is necessary for applying a (new) coating to a surface. The preparation ensures that the new layer will adhere well, which improves the durability of the coating in case the coating is depending on thorough cleanliness and a certain surface profile to long-term adhesion. To achieve this, old layers such as paint, mill scale, rust and other dirt need to be removed from the surface. Moreover, surface preparation not only removes dirt; it also creates a profile on the surface, which serves as an adhesion layer for the new coating.
The phases of surface preparation
Surface preparation has several phases. In order to achieve the best possible result, it is important – regardless of the technique used – that these phases follow each other closely and are carried out properly. In total, six steps can be distinguished:
1. Assessment of the condition
2. Coating removal
3. Removal of surface contaminants and restore imperfections
4. Removal of loose dirt
5. Apply adhesion profile to the surface
6. Dry the surface
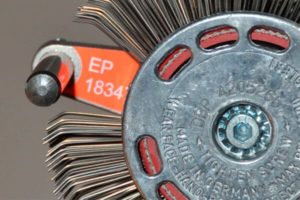
Assessment of the condition
Before the surface preparation can be started, it is important to assess the current condition of the material. Based on this, it can then be determined what needs to be done and what technique will be used for the surface preparation. If this is not done or done carelessly, it can cause damage to the material later in the preparation process.
Coating removal
Before the surface preparation can be started, it is important to assess the current condition of the material. Based on this, it can then be determined what needs to be done and what technique will be used for the surface preparation. If this is not done or done carelessly, it can cause damage to the material later in the preparation process.
Removal of surface contaminants
Not only the old coating; other dirt that has developed on the surface must also be removed. Over time, for example, rust, mill scale and other dirt may develop on the surface. As with the removal of the old coating, it is also important to remove these contaminants such as dirt, grease, fat and salts from the surface. If this is not done properly, it can also lead to adhesion problems of the new coating.
Removal of loose dirt
Besides the fact that rust, mill scale and other adhesion problems can occur, a surface often also has to deal with loose dirt. This can include flaking or crumbling pieces of the old coating. These too must be removed during the surface preparation process in order to ensure proper adhesion of the new coating.
Apply a surface profile to the surface
Once the old coating and all types of dirt have been removed, it is time to apply a new profile on the surface. When a proper new surface profile is applied, the new coating will adhere better than on a smooth surface in case a specific coating is depending on this anchoring profile.
Dry the surface
Once the adhesion profile has been applied to the surface, it is time for the sixth and final step of surface preparation: drying. New coatings will, in most cases, adhere better to a dry surface than to a wet surface. If the coating were applied to a wet surface, small grains will form in the material as it dries. To avoid this, it is necessary to dry the surface thoroughly first. If the six steps of surface preparation are performed accurately and carefully, the chances that the new coating will adhere nicely to the surface will be greatly increased.
Surface preparation techniques
Over the years, many surface preparation techniques have been developed. In most cases, traditionally, surfaces are mostly prepared by blasting, but dry cleaning and fire blasting are also possibilities. But how do these methods actually work, and what exactly do they involve?
Blast cleaning methods
One of the most common methods for surface preparation is blasting. The surface is prepared with a combination of air and a loose abrasive. Originally this was mostly done with sand, but this has been banned in many countries. Nowadays, blasting is also done with special abrasive grains or other materials. The grains have an abrasive effect on the surface, which removes rust and other dirt from the object. Blasting is not only used for the removal of dirt; the impact of the grains in the surface also creates an adhesion layer for the new coating.
One type of blasting is spray blasting. This technique is often used on the more vulnerable surfaces, but is in principle applicable to many materials. It works as follows: water is sprayed onto the surface with a rotating sprayer. This is not done under high pressure, but with mist jets, so that the spray slides over the object. Because of this low pressure with which the water is applied to the surface, this method of surface preparation is less efficient and also does not create a profile for the new adhesive layer.
You also have flame blasting. This involves holding a gas flame along the surface, which removes dirt and especially rust residue from the surface. However, this method of surface preparation is not very effective at removing all rust and often needs to be used alongside other techniques. In addition, improper use of the flame can quickly lead to surface damage with this type of surface preparation.
Chemical cleaning
Other common ways of preparing surfaces is chemical cleaning, which involves removing oil, dirt and other materials with detergents, solvents and other cleaners. This can be done with the following techniques:
– Degreaser/Cleaner: powerful cleaning solution that has to be poured directly onto the surface you want to clean. Then,
use a brush or cloth to scrub the solution onto the surface and rinse with water.
– Steam Cleaning: highly recommended for removing substances from large areas. Before applying any coatings, it is
crucial to ensure that the surface is completely dry and free from any residue.
– Alkaline Cleaning: effective for eliminating grease, fat, acid residue, oil, and other similar substances. With this
method, it’s also essential that the surface is completely dry and free from any residue before applying any coatings.
However, the chemical method of surface preparation can be very harsh due to the use of acid, both to the material and
to the environment and human health.
Preparing surfaces with power tools
MontiPower power tools are the solution to all your surface preparation problems. The tools of MontiPower do the same job as the usual techniques for surface prep, but better, more effective and without all the additional disadvantages.
Our specially designed technology with portable, semi-automatic machines not only ensures that the surface is cleaned, but also creates the roughness or surface profile for optimal adhesion layer for the new coating. It makes MontiPower’s power tools the alternative to ‘sandblasting‘ for smaller areas or when regulations do not allow the use of loose abrasives in the open field or where loose abrasive blasting is less productive.
We offer highly effective solutions for preparing surfaces with our Bristle Blaster®. Rust, paint, mill scale; removing the various types of dirt has never been easier. Moreover, with the use of MontiPower’s surface preparation tools, you are no longer dependent on external parties; from now on, you will be preparing surfaces all by yourself. With our wide range of rotating, patented bristles, you will always find a solution for your own specific situation at MontiPower. It makes an investment in MontiPower’s power tools the perfect investment that will save you both time and money in the short term.
Disadvantages of surface preparation
Some of the methods of surface preparation, like loose abrasive blasting and/or the use of chemicals, have been performed for many years. Yet, over the years, many of the disadvantages and dangers of sandblasting and various other methods have come to light.
Disadvantages of sandblasting
As mentioned earlier, “sandblasting” is a widely used technique for preparing substrates. However, the sand – or other blasting grains – in many cases are too cumbersome for smaller coating jobs. Because some materials are more difficult to process than others, it is recommended that this is always carried out by a professional. An intensive job, which also requires the necessary preparation, which makes sandblasting a relatively expensive way of surface preparation for smaller jobs in m2 per day. But that’s not all.
Sandblasting can be very harmful to the health of people and the environment from different perspectives such as Co2 impact. This danger lies mainly in the particles used in this process. Due to the high pressure involved in the blasting process, these particles break down into small particles. When inhaled, these particles can cause various health problems. The risks involved in sandblasting have caused this method of surface preparation to be banned in many countries, like for instance silica sand.
Disadvantages of chemical cleaning
With the chemical method of surface preparation, the danger lies in the acid that is used. This usually involves hydrochloric acid; a very aggressive agent, which can cause the necessary problems if it comes into contact with humans. In addition, when working with hydrochloric acid, a vapor is created that can be very dangerous for humans, animals, and the nearby environment.
Easy prep in various sectors
Their convenience and effectiveness makes the tools and bristles of MontiiPower widely used in various markets. Consider, for example, the production and maintenance of bridges, rail tracks, train wagons, and windmills. Infrastructure is a sector in which it is important that maintenance is not only done very well, but also safely and quickly.
Where traditional methods for surface preparation can be very labour-intensive and unsafe, MontiPower’s power tools actually contribute to a significant effect on health, safety and the economy. The same applies, for example, to surface preparation in the industrial sector, where gas and oil can be handled a lot, the marine sector, where the environment plays a major role or the welding industry, where it is very important both before and after the welding process to prepare and clean the steel properly for the durability of the object. It makes MontiPower’s power tools the solution for effective surface preparation in many situations.