Corrosion of steel pipelines
Corrosion of steel pipelines is a common process that is unfortunately difficult to counteract. To keep the condition of the pipelines intact, it is necessary to remove the corrosion in time. When the corrosion is more persistent, the choice is often made to replace the pipeline in its entirety. A demanding and also expensive job, costing billions of dollars per year worldwide.
There are various types of corrosion in pipelines. Each type has its own characteristics and ways to combat it. But what is corrosion exactly? How does corrosion occur in pipelines? And what are the different types of corrosion that we can distinguish?
What is corrosion?
Corrosion is a deterioration of metal as a result of a chemical process. This chemical reaction is caused by contact with various factors from the environment. Often corrosion is confused with rust. However, corrosion is a broader concept than corrosion. With rust, the deterioration of the surface occurs specifically through a reaction of oxygen in combination with damp. As a result, the well-known visible brown layer appears on the metal surface. With corrosion, this deterioration can be caused by a chemical reaction of several factors. There are various forms of corrosion in pipelines. But what are the most common types of corrosion in pipelines, and what characterizes these types of corrosion?
Oxygen corrosion
Oxygen corrosion is the other name for the already mentioned rust. It is the most common and also the most visible type of corrosion in pipelines. As mentioned, oxygen corrosion is caused by a chemical reaction between oxygen and water or another form of damp. From this reaction, a so-called oxide skin is formed, which we know better as the brown layer that attacks the metal surface. An important characteristic of the oxide skin of oxygen corrosion is the open structure of the layer. This ensures that oxygen and water continue to reach the surface easily, so that the steel will slowly but surely become completely corroded. For this reason, stainless steel or aluminum is used more often in various sectors; these materials have a denser oxide skin, which makes oxygen corrosion less likely to occur.
Uniform corrosion
Uniform corrosion is broadly comparable to oxygen corrosion. Uniform corrosion also results from a chemical reaction between damp and oxygen. This form is characterized by the – the name says it all – uniform distribution of the corrosion over the entire steel surface. Uniform corrosion is considered by many to be the least dangerous form of corrosion. By taking measurements or from previous experience, the speed and extent of corrosion formation can often be predicted well. As a result, the development and consequences of uniform corrosion can often be better estimated than those of other forms of corrosion in pipelines.
Acid corrosion
In the case of acid corrosion, the combination of acid and metal react together to form hydrogen gas and metal salt. To better understand this, it is good to first look at what is actually meant by acid. This has to do with the pH value of water. Normal drinking water has a pH value of between 7 and 9.5. Does the water have a pH value below 7? Then we speak of an acid. When this acid comes into contact with metal, corrosion occurs in the form of hydrogen gas and metal salt. The degree of corrosion depends on the tension of the material. Each material has its own voltage, which can cause a current to flow between several materials. If the voltage of the material has a lower voltage than hydrogen, acid corrosion occurs.
Galvanic corrosion
The voltage of metals that were briefly discussed in the case of acid corrosion also play a major role in galvanic corrosion. This type of corrosion can occur when two different metals are in close proximity to each other. If these metals come close together, in combination with water or a similar conductor, the reaction that is set in motion will result in corrosion. In this process, more corrosion will occur on the metal with a lower voltage than on the metal with a higher voltage.
Stress corrosion
Unlike, for example, oxygen corrosion, stress corrosion is very difficult to predict and only detect at a late stage. This form of corrosion occurs particularly with tension from within, for example with dents or welds. But this is not the only factor involved in stress corrosion. When the combination of chlorides, high temperatures and internal tension come together, stress corrosion will occur, and the material will crack. Whereas oxygen corrosion and uniform corrosion occur less quickly and frequently in RVS, stress corrosion occurs more frequently in RVS.
Stray current corrosion
Stray current corrosion is a form of corrosion similar to galvanic corrosion. Stray current is electric current that flows from a conductor back to the soil or surrounding environment. The difference from galvanic corrosion is in the fact that it is not the other metal, but the actual current from the conductor that causes corrosion to occur in the steel pipeline.
Pitting Corrosion
Pitting corrosion occurs in the oxide layer that may have developed in the steel pipeline. This form of corrosion occurs mainly in the areas where the oxide layer is damaged. In addition, pitting corrosion can also occur as a result of the incorporation of chloride ions or metal particles. The corrosion that occurs in the oxide layer causes small pits to form in the steel, but these are often barely detectable at first glance.
Crevice corrosion
Similar to pitting corrosion is crevice corrosion. In this case, the corrosion does not occur in damaged surface, but in cracks. When the surface comes into contact with a conductor and also makes electrical contact with the crack, crevice corrosion will occur. As with pitting corrosion, the corrosion will develop more and more strongly and the crack will become deeper and deeper.
Intergranular corrosion
Intergranular corrosion is one of the most insidious forms of corrosion. Due to the fact that this type of corrosion is molecular, it is not or hardly visible to the naked eye. On the surface of the steel pipeline, little or no corrosion occurs, but from the inside the material is increasingly corroded. This causes the metal to become increasingly brittle, which in turn causes the metal to lose its cohesion and may eventually cause major damage.
Microbial corrosion
Microbial corrosion is one of the most unknown forms of corrosion. Nevertheless, this form of corrosion is very relevant to steel pipes, as microbacterial corrosion is especially common in pipelines. This has to do with the fact that in most cases, the bacteria thrive in oxygen-free spaces. The corrosion is caused by the bacteria secreting a substance, which has a corrosive effect on the steel. Microbacterial corrosion is most comparable to acid corrosion, but in this case the corrosion is not caused by an acid but by the bacteria.
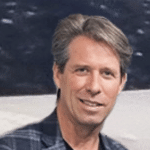
Frits Doddema
Author of MontiPower®
Leadership | Sales | Marketing | Development
He is passionate about alternating solutions which make a true difference. Nothing is impossible is his credo. To make the impossible possible, Frits and the management believe in just one idea to make it happen and to turn the company in a great firm. The innovative approach for game-changing blasting and paint solutions is hands-on keeping in mind the difficult field circumstances for operators, respecting nature and long term costs. The mission is to avoid any disagreement over quality of prep work and coating. Frits and his team push for non-hazardous long term corrosion prevention solutions to overcome any hassle out of a coating job ensuring the best possible bond. The world’s best coatings deserve the world’s best surface preparation. Like in daily life, preparation is everything. From different perspectives like Safety, Health, Ergonomics, Productivity, Recyclability, Co2 neutrality of the plant and the coating process, Substrate Compatibility, Corrosion Resistance, Frits and team are driven to come with improved unique contribution solutions to existing and new end markets.