Abrasive blasting: everything you need to know
Abrasive blasting is a technique that has been used for many years. Although using loose abrasives for blasting is a very common practice, this method also has its drawbacks. These disadvantages are a thing of the past with the power tools from MontiPower for spotrepair and maintenance.
In this article, we will tell you everything you need to know about abrasive blast cleaning. And moreover, what are those drawbacks? And how do MontiPower’s power tools serve as an alternative for loose abrasive blasting?
What is abrasive blasting?
What is abrasive blasting exactly? In simple terms, abrasive blast cleaning refers to the process of using pressurized air, combined with either dry abrasive particles or abrasive particles mixed with water, to shoot at a part or surface. This technique is also known as sandblasting or grit (garnet) blasting, because silica sand is (one of) the most popular abrasives. Blasting with abrasives is often used to clean, treat or process different types of surfaces – such as steel or other metals.
Traditionally, sandblasting has been the most commonly used method of blasting. Over the years, more and more different techniques are available to replace this. Think of blasting with, for example, steel grit, glass or plastic. The blasting media, in combination with air, is blasted onto the object with great force. Broadly speaking, all these ways of abrasive blasting work in the same way.
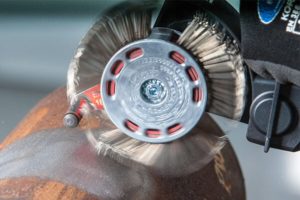
What is abrasive blasting used for?
Now you know what it is, but what is abrasive blasting used for? Due to the impact of the blasting material, a layer gets removed from the surface. The use of abrasives during blasting creates a hammering effect, which can remove rust, mill scale, lacquer and other coatings from the surface. This not only cleans the object, but also creates a structure in the surface, which can serve as an adhesive layer for a new coating. In short, if you’re looking for a way to clean surfaces and prep them, abrasive blasting is a commonly known practise as per the ISO and AMPP standards for thorough cleanliness results.
Health risks and other dangers
The use of sand in blast cleaning is decreasing further and further. This is due to health risks and other dangers, which have increasingly come to light over the years. In some countries, including the Netherlands, it is even forbidden to blast with sand because of the dangers. Research showed it’s harmful for the health of humans and animals.
Due to the great force with which sand is blasted onto the surface, these sand grains break down into minuscule pieces. The particles are so small that they can easily be inhaled, causing respiratory and other health problems.
Alternative tools to abrasive blasting: the Bristle Blaster® and MBX®
The Bristle Blaster® and MBX® from MontiPower are the new developments in the field of surface preparation. Due to the specially developed technology with patented brushes, the power tools are the perfect alternatives for the existing blasting equipment.
With the use of the Bristle Blaster® and MBX® from MontiPower, blasting with different types of loose abrasives is a thing of the past for smaller areas and difficult to access areas. The tools are easy to use, are – unlike blasting – completely safe and very effective. Not only in cleaning surfaces, but also in processing them.
With their impact, the brushes of the power tools create a profile on the surface that can be compared to the surface profile that is created after blasting. In this way, MontiPower tools are the ideal alternative to sandblasting.
How do MontiPower abrasive brushes work?
The Bristle Blaster® and MBX® from MontiPower are hand-operated tools, which are equipped with a rotating brush. These specially designed brushes are characterized by their sharpened flexible tips with kneed ends.
By rotating the brushes at a low RPM, the different types of surfaces are processed and cleaned easily, quickly and effectively. The kneed tips of the brushes play an important role in this. These points are held back for a very short time during the rotation of the Bristle Blaster Brush by the so-called ‘accelerator bar’. Due to this short interruption, the points – partly due to the high speed at which the brush rotates – are released with great power from behind the accelerator bar. This technique ensures that the curved tips of the brushes are immediately retracted upon contact with the surface, effectively cleaning the surface and also providing it with the characteristic micro-structure. It makes MontiPower tools the ideal surface preparation method for many sectors, and a great alternative to blasting with abrasives.
Alternative to blasting with abrasives in different sectors
With their many advantages, our power tools ensure that they are the ideal alternative to cleaning with abrasives for many markets. As mentioned, the traditional ways of blasting can be harmful to humans and animals, but also damaging to the environment. It makes the Bristle Blaster® and MBX® from MontiPower, among other things, an excellent alternative for surface preparation in the maritime and industrial sector.
In addition, the convenience and effectiveness of the various power tools play an important role in many sectors. A good example of this is the work in public infrastructure. The blasting of bridges, tracks and highways, among other things, is a very time-consuming and labor-intensive job, which is subject to a lot of pressure because of the time. When blasting these objects, workers are also exposed to various small particles and possible chemicals. With the use of the Bristle Blaster® and MBX® from MontiPower, abrasive blasting is a thing of the past.
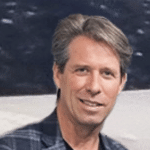
Frits Doddema
Author of MontiPower®
Leadership | Sales | Marketing | Development
He is passionate about alternating solutions which make a true difference. Nothing is impossible is his credo. To make the impossible possible, Frits and the management believe in just one idea to make it happen and to turn the company in a great firm. The innovative approach for game-changing blasting and paint solutions is hands-on keeping in mind the difficult field circumstances for operators, respecting nature and long term costs. The mission is to avoid any disagreement over quality of prep work and coating. Frits and his team push for non-hazardous long term corrosion prevention solutions to overcome any hassle out of a coating job ensuring the best possible bond. The world’s best coatings deserve the world’s best surface preparation. Like in daily life, preparation is everything. From different perspectives like Safety, Health, Ergonomics, Productivity, Recyclability, Co2 neutrality of the plant and the coating process, Substrate Compatibility, Corrosion Resistance, Frits and team are driven to come with improved unique contribution solutions to existing and new end markets.