What is welding and what techniques are used?
Welding is a joining technique used to make two materials into one. When materials are welded, they are joined together under very high temperatures, combined with high pressure. In the process, a small portion of the material is liquefied to allow for the attachment of both objects. By using two virtually identical materials, continuity is created between the two objects. Welding is mainly used when joining steel objects, but can also be applied to stainless steel, aluminum and some plastics, for example. For the welding process to be successful, the materials must at least be fusible.
Different welding techniques
Although in most cases, welding is done in the same way, there are different welding techniques. Which welding technique can best be used in which situation depends on the situation and the purpose of the materials. In order to explain the differences between the various welding techniques, we will take a closer look at the three most common methods of welding.
Electrode Welding
Electrode welding is also known in the world of welding as clad electrode welding or arc welding. This method of welding is mainly used when welding steel and stainless steel. It is unsuitable to use for aluminum. In electrode welding, you use a welding machine in combination with a package of covered electrodes. These electrodes are intended as an additive material in the welding process and will melt to the object as the process progresses. This melting process will then produce slag on the steel object. Slag is a brittle material that, in most cases, is created because the steel material has not been sufficiently cleaned of dirt, rust, paint or other coatings beforehand. This slag can be removed after the welding process is completed. Because the electrodes are coated, the use of a shielding gas, which is often required in other welding methods, is not necessary in this case. This makes electrode welding one of the few blasting methods that can be carried out outdoors. Another advantage of electrode welding is that it is relatively inexpensive and easy to carry out. This makes electrode welding the most suitable welding technique for home improvement projects and quick welding jobs where the appearance of the end result is relatively unimportant.
TIG welding
Another commonly used method of welding is TIG (Tungsten Inert Gas). Whereas electrode is mostly used by home handymen and relatively quick, easy welding jobs, TIG welding is generally labeled as the most difficult welding technique. This is due to the fact that in TIG welding, when adding the filler metal, two hands are required throughout the welding process. While one hand is holding the welding torch, the other is adding the filler metal. This makes TIG welding more difficult to perform and also takes a relatively long time. On the other hand, TIG welding, when performed properly, gives the most beautiful result in terms of appearance. When detailed welding jobs have to be carried out, where appearance is an important factor, TIG welding is the preferred technique. In addition, TIG welding is a very clean way of welding, where slag and other debris will not readily form.
MIG/MAG welding
The welding technique that is generally considered the easiest is MIG/MAG welding. MIG-welding (Metal Inert Gas) and MAG-welding (Metal Active Gas) differ only in the type of gas used, but otherwise they work in exactly the same way. The welding technique is characterized by the use of a constant voltage, which creates an arc between the welding wire and the material. The welding wire serves primarily as an electrode, but when it melts it also serves as a filler material, making MIG/MAG welding a relatively much faster welding technique than the other methods of welding. As a result, MIG/MAG is one of the most widely used welding techniques in the welding industry and at large companies. However, given the fact that MIG/MAG is not allowed to be used outdoors and the material is also relatively expensive, this is not a technique that will be quickly employed by a home handyman. In addition, the amount of dirt is also relatively high compared to, for example, TIG welding.
Welding: the advantages and disadvantages
Welding is not the only way to attach two materials together. A connection with a bolt and a nut, for example, is also a possibility. Nevertheless, a welded joint has several advantages compared to other ways of joining.
First of all, a welded joint is very strong. Because there is continuity in both objects, the connection is hardly noticeable and one can rightly speak of a solid whole. In addition, a welded joint is relatively easy to apply. Whereas, when creating a connection using bolts and nuts, holes first need to be made in the material, this is not necessary when welding.
Although welding has many advantages, there are also disadvantages. A welded joint is permanent and cannot be disassembled. On the one hand, this can be seen as a great advantage, but when the various parts have to be disassembled after some time, it can still turn out to be a disadvantage. In addition, welding is not possible with all materials. As mentioned, welding is mainly carried out with steel, stainless steel and aluminum, but it is only possible when two more or less the same materials are used. When two different materials have to be joined together, welding is not an option. Also, as mentioned earlier, different welding techniques can produce slag and other debris, which must be cleaned after the welding process. Fortunately, MontiPower’s power tools offer the solution.
Welding cleaning with the Bristle Blaster® and MBX® MontiPower
The Bristle Blaster® and MBX® from MontiPower are the revolutionary tools in the field of surface preparation and cleaning. The hand-held tools are not only suitable for removing rust, coatings and dirt, but can also be used in weld cleaning, for removing slag and other residue. The precise and effective action of the rotating brush of the Bristle Blaster® and MBX® ensure thorough contamination without damaging the material. Not only after the welding process has been completed; cleaning of the metal may also be required before welding begins. When the object is covered with mill scale, rust or other dirt, its removal is necessary to achieve a perfect result. The power tools provide, both before and after the welding process, a fast, effective and also very easy cleaning.
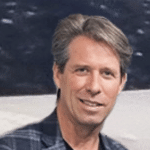
Frits Doddema
Author of MontiPower®
Leadership | Sales | Marketing | Development
He is passionate about alternating solutions which make a true difference. Nothing is impossible is his credo. To make the impossible possible, Frits and the management believe in just one idea to make it happen and to turn the company in a great firm. The innovative approach for game-changing blasting and paint solutions is hands-on keeping in mind the difficult field circumstances for operators, respecting nature and long term costs. The mission is to avoid any disagreement over quality of prep work and coating. Frits and his team push for non-hazardous long term corrosion prevention solutions to overcome any hassle out of a coating job ensuring the best possible bond. The world’s best coatings deserve the world’s best surface preparation. Like in daily life, preparation is everything. From different perspectives like Safety, Health, Ergonomics, Productivity, Recyclability, Co2 neutrality of the plant and the coating process, Substrate Compatibility, Corrosion Resistance, Frits and team are driven to come with improved unique contribution solutions to existing and new end markets.