Galvanized steel is a widely used material in many industries. But what is galvanized steel, how does it differ from non-galvanized steel and what are the different ways of galvanizing steel.
What is galvanized steel?
There are many advantages to using steel in general. For example, steel can be used in many situations and is known for its strength. Yet, it also has disadvantages. For example, steel can rust over time, which reduces the quality and appearance of the steel object. To counteract this, the steel can be galvanized. This involves applying a thin layer of zinc to the steel by means of a chemical process. This protective layer ensures that the steel is less likely to rust, making the material last longer. In addition, zinc coating makes the surface less likely to be scratched, which is why many people find galvanized more attractive than the non-galvanized variety.
Ways of galvanizing steel
When steel is brought into contact with molten zinc, a chemical reaction occurs, causing the zinc to adhere to the steel surface. Over the years, different ways have been developed to initiate this galvanizing process. The technique most commonly used for this is termite galvanizing. This involves immersing the steel in molten zinc at a temperature of around 460 degrees Celsius, whereby the chemical reaction mentioned earlier takes place and the protective zinc layer adheres to the steel surface.
Other common techniques for electroplating steel are:
- Electrogalvanizing: this involves placing the steel in a zinc solution, after which an electric current is passed through it. This creates a relatively thin but very strong and uniform galvanizing layer.
- Mechanical plating: the steel is stirred together with zinc powder and a special galvanizing agent in a drum. Because the different materials touch each other during this process, a thin layer will be formed on the steel.
- Scraping: this involves passing zinc through a spray gun in which it is liquefied. The liquid zinc can then be applied to the steel with the spray gun, provided it has been cleaned properly in advance.
- Diffusion galvanizing: the steel is heated to around 400 degrees Celsius together with a zinc powder. The diffusion process that is hereby set in motion between the zinc and the steel ensures that an even layer of zinc is applied to the steel.
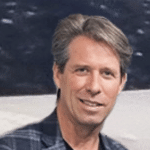
Frits Doddema
Author of MontiPower®
Leadership | Sales | Marketing | Development
He is passionate about alternating solutions which make a true difference. Nothing is impossible is his credo. To make the impossible possible, Frits and the management believe in just one idea to make it happen and to turn the company in a great firm. The innovative approach for game-changing blasting and paint solutions is hands-on keeping in mind the difficult field circumstances for operators, respecting nature and long term costs. The mission is to avoid any disagreement over quality of prep work and coating. Frits and his team push for non-hazardous long term corrosion prevention solutions to overcome any hassle out of a coating job ensuring the best possible bond. The world’s best coatings deserve the world’s best surface preparation. Like in daily life, preparation is everything. From different perspectives like Safety, Health, Ergonomics, Productivity, Recyclability, Co2 neutrality of the plant and the coating process, Substrate Compatibility, Corrosion Resistance, Frits and team are driven to come with improved unique contribution solutions to existing and new end markets.