VAPOR BLASTING
Vapor blasting is a type of abrasive blasting that combines water with an abrasive material like glass beads, aluminum oxide, or crushed glass to prepare and clean surfaces.
WHAT IS VAPOR BLASTING
Different techniques are possible for preparing and cleaning different types of surfaces. One of the techniques most commonly used for this is abrasive blasting. Vapor blasting is similar to other abrasive blasting methods, but has one important difference: while abrasive blasting uses abrasive media in combination with air (e.g. sandblasting), water is added in the case of vapor blasting. Because of the relatively low force involved, vapor blasting is mainly used to remove light pollution from, for example, facades and walls, but water blasting can in most cases also be used to remove rust, mill scale, copper slag, coatings and other dirt.
HOW DOES A VAPOR BLASTING MACHINE WORK?
Two elements are required to use a vapor blasting machine: water and an abrasive. In most cases, sand is added to the water, but nowadays there are also special abrasives that can be used in this process. The water and the abrasive are mixed inside the blast machine and the mixture is then applied to the surface. The pressure of the machine can be adjusted, but will at all times be much lower than with other blasting methods. Because of the low pressure used, there is no powerful jet directly on the surface, but the abrasive material gradually slides over the surface. This makes vapor blasting especially suitable for preparing more vulnerable surfaces and for removing light pollution.
VAPOR BLASTING VS. DRY BLASTING
Vapor blasting and the dry variants of abrasive blasting can be compared in many ways. The main difference lies in the fact that with vapor blasting, water is added to the abrasive. The water has, as it were, an attenuating effect on the abrasive and therefore a much less aggressive effect on the surface than dry blasting. With coarser pollution, dry blasting is often preferred over vapor blasting. For more delicate materials, however, vapor blasting is an excellent alternative to sandblasting . Another major advantage of vapor blasting over dry blasting is the minimal amount of dust that is released during preparation of the surface. With dry blasting, the abrasive hits the surface harder, breaking up the material into small pieces and can create a lot of dust. Due to the low force plus the fact that water is added, the amount of dust is kept to a minimum with vapor blasting.
ADVANTAGES OF VAPOR BLASTING
Vapor blasting creates a powerful combination of steam and abrasive material to clean, erase, and smooth any surface it comes in contact with. It produces less dust and therefore provides a much cleaner working environment. Vapor blasting is less risky to use and also reduces the amount of energy needed to operate the machine.
DISADVANTAGES OF VAPOR BLASTING
Vapor blasting has a number of major advantages. For example, the use of vapor blasting machines is extremely suitable for use on fragile surfaces and dirt can be removed very precisely. Nevertheless, vapor blasting also has a number of disadvantages compared to other methods of surface preparation. For example, is a surface heavily stained with rust, paint or other coatings? Then, due to the relatively low power, this is often not completely removed when using vapor blasting. In line with this, there is another disadvantage of vapor blasting. When a steel surface is stripped of dirt and coatings by means of a dry blasting technique, the relatively hard impact of the abrasive creates a surface profile in the prepared material. This profile can then serve as an adhesion layer for the coating to be applied. Because the force of this impact is much lower with vapor blasting, this profile will be created to a much lesser extent. This is why dry blasting is preferred in many cases, although it also has its disadvantages.
ALTERNATIVE TOOLS FOR VAPOR BLASTING
When it comes to fragile surfaces, vapor blasting is an excellent option. When there is more severe soiling, dry blasting is often preferred. However, there are also disadvantages to both vapor blasting and dry blasting. Dry blasting is often too aggressive, which can cause damage, and both blasting methods are also difficult to carry out yourself. Therefore, it is always advised to let a professional do it, which makes blasting a relatively expensive job.
With MontiPower’s Bristle Blaster® and MBX®, the alternative tools for vapor blasting and dry blasting are now on the market. The manually operated tools offer all the advantages of both blasting methods, excluding all the disadvantages that come with it. The machines are easy to operate by themselves, have an effective and powerful operation and, moreover, do not contain any harmful abrasives. Both vapor blasting and dry blasting are therefore forever a thing of the past with the arrival of the Bristle Blaster® and MBX®.
SURFACE PREPARATION WITHOUT VAPOR BLASTING WITH MONTIPOWER’S POWER TOOLS
Certain standards apply to the surface preparation of steel. Normally, the use of industrial coatings requires a surface cleanliness of Sa 2.5 (or SSPC-SP10 or NACE 2) and a specific roughness based on the surface preparation standards. In most cases, abrasive grit blasting is used for this purpose. ‘Sand blasting’ has traditionally been the best known method of grit blasting, but nowadays, grit blasting can also be done with other materials. But how does surface preparation with grit blasting actually work? What types of grit blasting are there, what are the advantages and disadvantages, and how are MontiPower’s power tools a good alternative for this?
ALTERNATIVE FOR VAPOR BLASTING: THE BRISTLE BLASTER®
The Bristle Blaster® is MontiPower’s alternative to grit blasting. The grit-free patented Bristle Blaster® is able to produce a surface quality comparable to grit blasting both in cleaning of the object and in roughness capacity:
– surface cleanliness of Sa 2.5 or SSPC-SP 10
– roughness capacity up to 120 μm Rz (ca. average 65-83 μm Rz on API 5L steel)
The major advantages of the power tools over traditional blasting methods are their simplicity in use and their relatively low cost. This is because the surface is prepared with a light, handheld machine. Other alternatives to grit blasting that are used to work smaller areas are also unable to prepare a surface profile suitable for industrial coating. In addition, these other alternatives to grit blasting usually cannot meet the surface cleanliness and roughness requirements, which is possible with the Bristle Blaster®.
Bristle Blasting is ideally suited for portable usage as no protective suits with closed system respiratory equipment are required and no complex machinery or other grit media recovery equipment is needed. Only the application of standard personal protective equipment (PPE) is recommended for the eyes, face, hands and respiratory. Apart from the materials removed, no other additional or environmentally harmful waste products are produced.
HOW DO THE ALTERNATIVE VAPOR BLASTING TOOLS WORK?
MontiPower’s alternative grit blasting tools are manually operated tools equipped with a rotating brush. Due to the specially designed curved brush tips, the surface is cleaned quickly and easily, with similar results to traditional grit blasting. Because the tips are released with a great deal of force from behind the tools’ accelerator bar, they immediately retract from the surface, providing the same roughness as with grit blasting. In this way, the Bristle Blaster® offers all the advantages of grit blasting, including the high-quality result. This makes MontiPower power tools for many markets the relatively cheap, easy to operate and effective alternative to the traditional grit blasting machine.
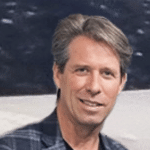
Frits Doddema
Author of MontiPower®
Leadership | Sales | Marketing | Development
He is passionate about alternating solutions which make a true difference. Nothing is impossible is his credo. To make the impossible possible, Frits and the management believe in just one idea to make it happen and to turn the company in a great firm. The innovative approach for game-changing blasting and paint solutions is hands-on keeping in mind the difficult field circumstances for operators, respecting nature and long term costs. The mission is to avoid any disagreement over quality of prep work and coating. Frits and his team push for non-hazardous long term corrosion prevention solutions to overcome any hassle out of a coating job ensuring the best possible bond. The world’s best coatings deserve the world’s best surface preparation. Like in daily life, preparation is everything. From different perspectives like Safety, Health, Ergonomics, Productivity, Recyclability, Co2 neutrality of the plant and the coating process, Substrate Compatibility, Corrosion Resistance, Frits and team are driven to come with improved unique contribution solutions to existing and new end markets.