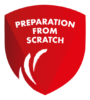
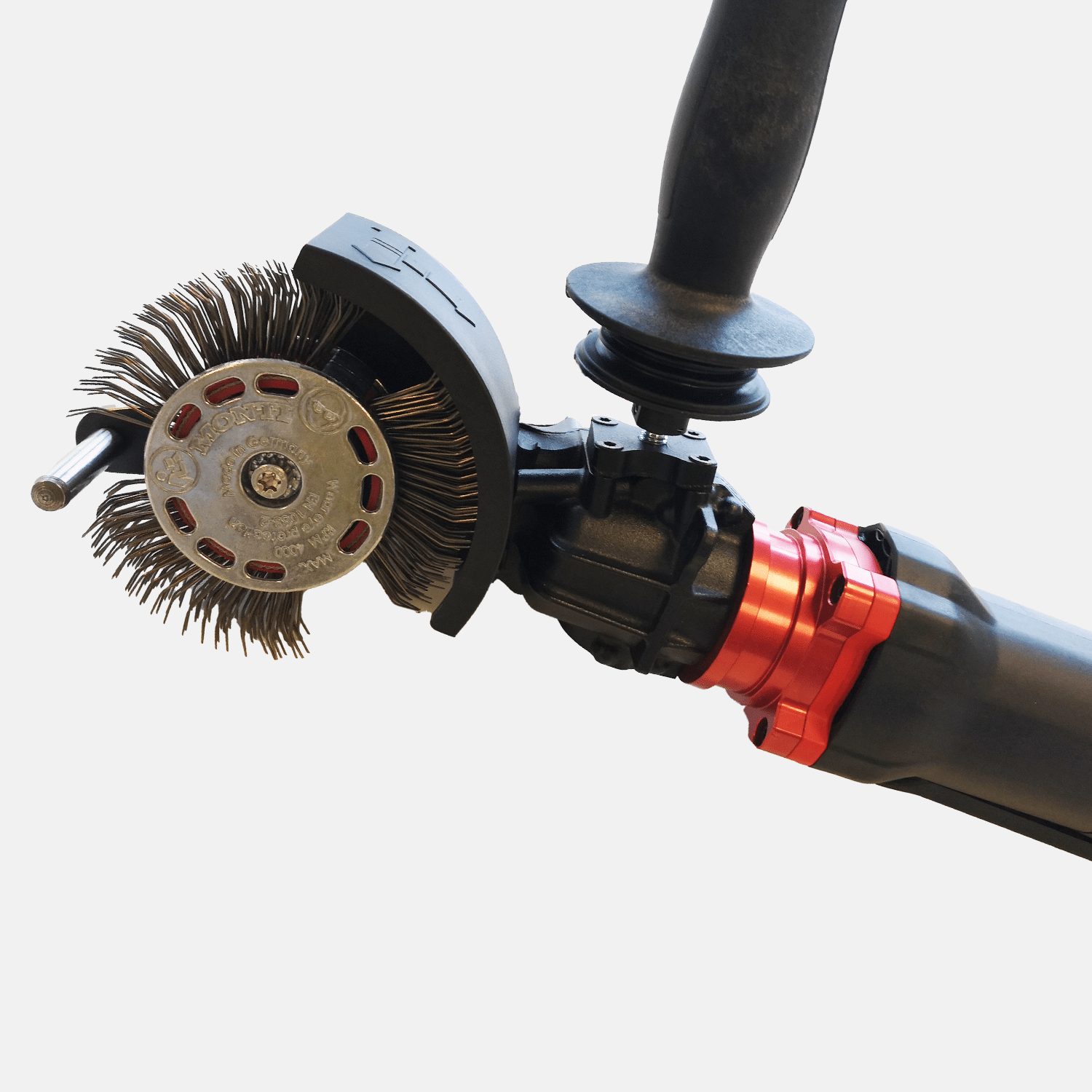
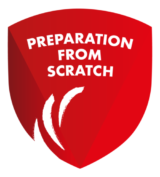
BRISTLE
BLASTER®
ULTIMATE ELECTRIC
Removes corrosion and generates an anchor profile by using a specially designed rotary bristle tool
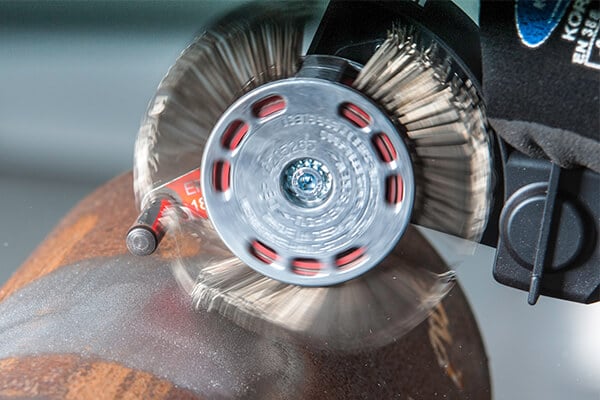
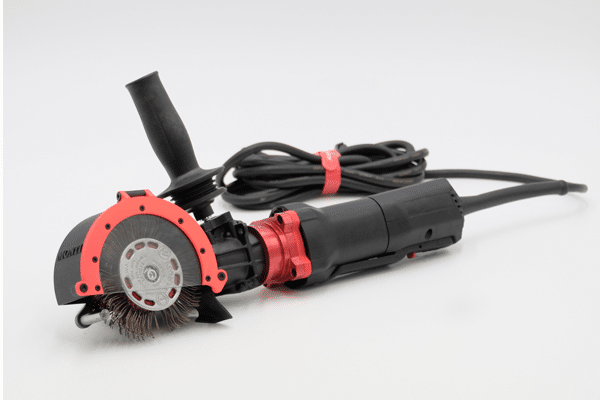
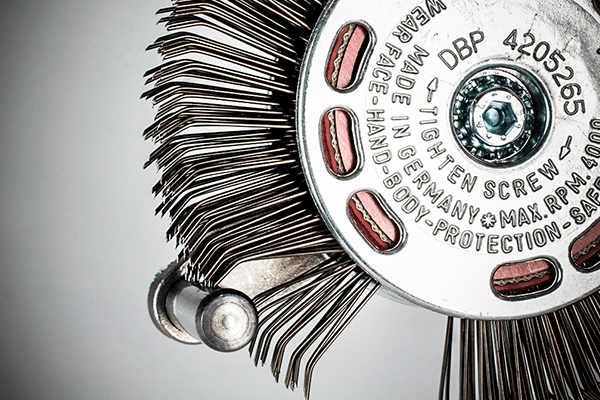
BRISTLE BLASTER® ULTIMATE ELECTRIC
Bristle Blasting technology simultaneously removes corrosion and generates anchor profile.
The bristle tips are designed to strike the corroded surface with kinetic energy that is equivalent to standard processes that use grit blast media.
Immediately after the bristle tips strike the surface, they retract (“rebound”) from the surface, which results in both corrosion removal and micro-indentation that exposes fresh surface.
Consequently, surfaces that have been treated by Bristle Blasting have a texture and visual cleanliness that mimics those obtained by traditional grit blasting processes.
Specifications
Belts
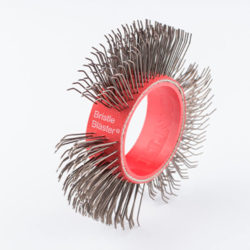
Steel, 23 mm
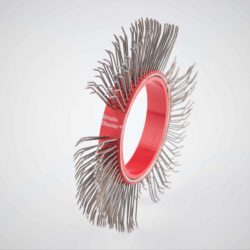
Steel, 11 mm

Stainless Steel, 23 mm
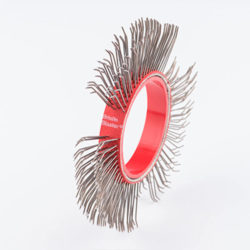
Stainless Steel, 11 mm
Accessories
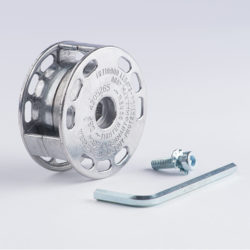
Adaptor System 23 mm
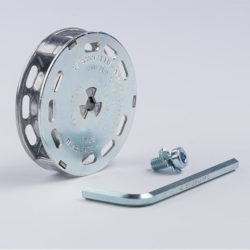
Adaptor System 11 mm
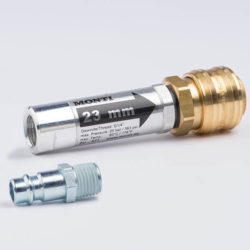
Air Pressure Regulator 23 mm
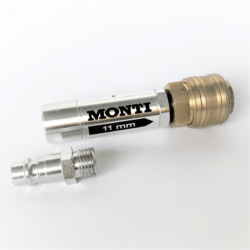
Air Pressure Regulator 11 mm
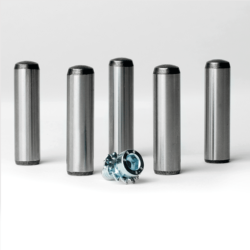
Accelerator Bar Steel 23 mm

Accelerator Bar Steel 11 mm
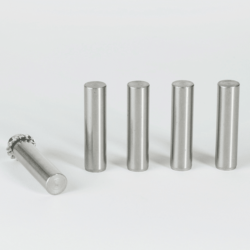
Accelerator Bar Stainless Steel 23 mm
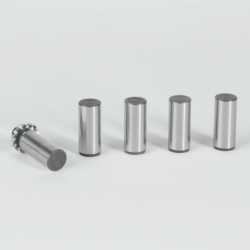
Accelerator Bar Stainless Steel 11 mm
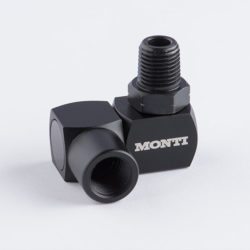
Swivel Connector
Boxes
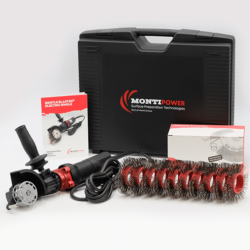
Bristle Blaster® Ultimate Electric Set, packed into a blow mould storage case
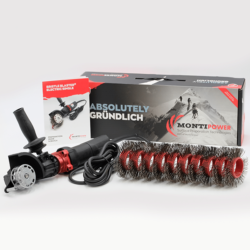
Bristle Blaster® Ultimate Electric Set, packed in a portable cardboard box
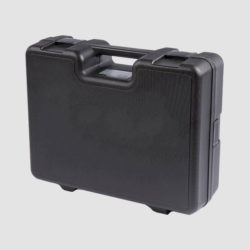
Jobsite Toolbox
Bristle Blaster® Ultimate Electric
The Bristle Blaster® Ultimate Electric is also available as standalone (without the extra belts and case)
Downloads
Frequently asked questions
Bristle Blaster®
What results does the Bristle Blaster® Technology deliver?
The patented Bristle Blaster® Technology is capable of removing corrosion and coatings quickly and thoroughly. At the same time, the Bristle Blaster® creates surface preparation grades comparable with Sa 2½–3 and roughness levels of up to 120 µm Rz.
Example: Roughness levels of 65–83 µm were achieved on a pipe made of API-5L-X42 steel with rust grade D.
What is the working speed of the Bristle Blaster®?
The working speed of the Bristle Blaster® depends on the following factors:
- Hardness and quality of the base material
- Rust grades present (A, B, C, D)
- Coatings applied (type, thickness)
- Scale layer
- Adhesive residues
Example: A working speed of 1.1 m² per hour was achieved on a pipe made of API-5L-X42 steel with rust grade B.
How long is the service life of a Bristle Blaster® Belt, an Accelerator Bar and an Adaptor System?
The average service life of a Bristle Blaster® Belt is approximately one hour which is about 1 – 1.5 m2 of the surface. Light flashrusted surfaces can be treated at a rate of 1.1 m2 per hour. On some applications e.g. surface preparation on plain weld seams, not coated, construction steel etc. even lifetime of Bristle Blaster® Belts up to 3 m2 has been experienced.
We roughly estimate that an Accelerator bar and an Adaptor system ought to be changed after having used approx. 50 Bristle Blaster® Belts.
The following factors affect the rate of wear:
- Hardness and quality of the base material
- Actual conditions of the substrate to be treated such as grade of corrosion (A, B, C, D)
- Coatings applied (type, thickness, hardness)
- Scale layer
- Adhesive residues
- Surface Shape
- Correct handling of the tool by the operator
What applications are Bristle Blaster® Belts made of stainless steel used for?
Bristle Blaster® Belts made of stainless steel are used exclusively to prepare nonferrous metals, such as aluminum and stainless steel. Together with the matching Accelerator Bars made of stainless steel, they prevent the surface being prepared from becoming contaminated and the contact corrosion this would lead to.
Can I also use Bristle Blaster® Belts on other drive units?
No! Bristle Blaster® Belts can only be used on MONTI’s Bristle Blaster® Pneumatic and Electric drive units. These drive units are equipped with an Accelerator Bar that increases the kinetic energy of the bristles many times over. What’s more, they are specially matched in respect of speed and torque for use with Bristle Blaster® Belts. Bristle Blaster® Belts only produce the desired results when used with the Bristle Blaster® drive units.
Why is the compressed-air supply so important to the functionality of Bristle Blaster® technology?
The Air Pressure Regulators supplied with the set regulate the optimum operating pressure and therefore the rotational speed of the Bristle Blaster®. If this speed is too fast, the individual bristle tips cannot strike the base material properly: All they do is scrape across the surface and they fail to generate the necessary surface roughness. The Air Pressure Regulators included in the scope of delivery of the Bristle Blaster® Pneumatic guarantee the ideal operating pressure for our technology: 6.2 bar for 23 mm belts and 5.2 bar for 11 mm belts.
What servicing work does the Bristle Blaster® need?
Pneumatic
The compressed-air motor of the Bristle Blaster® Pneumatic must be lubricated every time before it is used. All you have to do is put a few drops of low-viscosity oil into the compressed-air connection. Proper lubrication ensures that the tool enjoys a longer service life and is a precondition for warranty claims.
Electric
This tool should only be serviced by specialists trained in the repair of power tools or by other appropriately qualified tool servicing staff. Always make sure that the tool is switched off and disconnected from the power supply before carrying out servicing work.
Clean the motor housing every time after using the tool and, in particular, blow out the fan with compressed air to remove any dust.
Why has my Bristle Blaster® band torn?
If a Bristle Blaster® Belt tears at the seam, it has probably be used together with a worn adapter system. As time passes, this forms a sharp edge at the webs that connect the two shells. These sharp metal edges can cut the seam and destroy the belt. Consequently, an adapter system should be replaced after approximately 50 operating hours.
Where can I find instructions on how to use the Bristle Blaster®?
It is essential that you know how to work correctly with Bristle Blaster® Technology. You can find appropriate instructions in the user manual. We also recommend that you watch our application film.
Why do I need to attend a product training session?
Bristle Blaster® Technology requires that it is used in accordance with specific guidelines and in a certain way. We would like to teach you this by offering you a product training seminar.
Where can I buy a Bristle Blaster®?
We market our patented Bristle Blaster® Technology through a global network of importers. We serve the German market ourselves. Our subsidiary, MONTI Tools Inc., in Houston/Texas, is responsible for the North American market.
No matter where you purchase your Bristle Blaster®, you can expect to be welcomed by a competent partner, who will provide you with excellent personal aftersales service in addition to obligatory product training. You can find all our distributors here.
What is the difference between the Bristle Blaster® and the MBX®?
Bristle Blaster® and MBX® make use of two different technologies and are not compatible with one another.
The patented Bristle Blaster® is capable of removing corrosion and coatings quickly and thoroughly. At the same time, it creates surface preparation grades comparable with Sa 2½–3 and roughness levels of up to 120 µm Rz on appropriate steel surfaces.
The MBX® has been designed for use in automobile workshops and paint shops. Its wide range of belts caters for different tasks, such as removing underseal, sealants, rust and paint from bodywork.