Dr. Prepper
edition 5
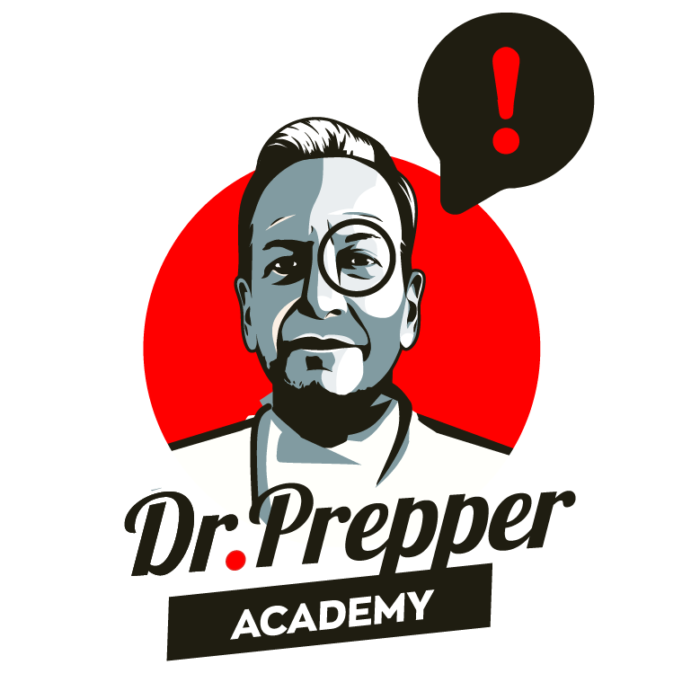
Compressive Residual Stress generated by Bristle Blasting Process with Implication upon Stress Corrosion Cracking
In this 5 th edition Dr. Prepper presents the abstract summarizes of Professor Stango’s work published by NACE International, addressing key aspects of surfaces that are generated by the Bristle Blasting process.
Important differences are discussed between striation-based (e.g., grinding or power brushing) and crater-based processes (e.g., abrasive blasting or Bristle Blasting). Special emphasis is placed on examining compressive residual stresses that are generated during the Bristle Blasting process and it’s repercussions on component life.
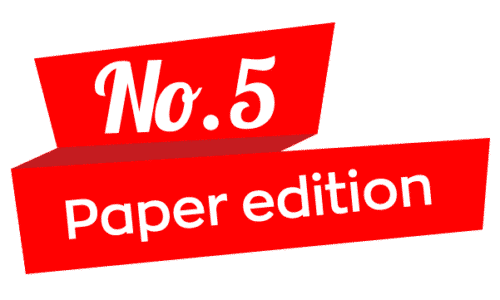
The regular RED PAPER from MontiPower®. Full of nice to know – and need to know – facts about the most optimal surface preparation since 1987.
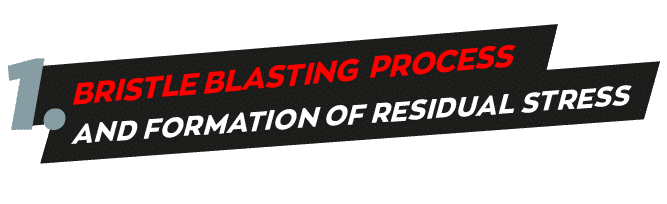
Striation-based surface preparation is characterized by score markings due to extended sliding contact duration between abrasive media and metallic surface. Thus, workpiece surfaces are subjected to greater material removal rates and frictional heating.
Excessive temperature can even lead to burn marks, also referred to as grinding burn, and is known to create extreme tensile residual stress that reduces the component life and increases susceptibility to stress corrosion cracking (ssc). 1
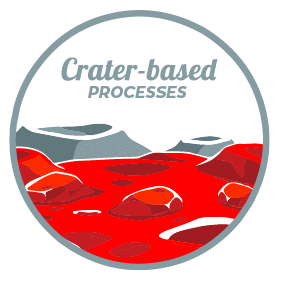
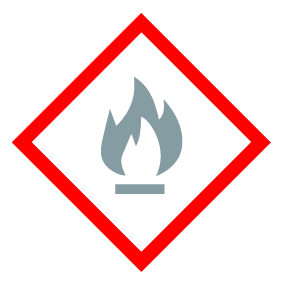
In contrast, crater-based processes generate minimal frictional heat, and create anchor profiles that are deemed essential for the subsequent adhesion and stability of applied protective coatings. Surface fragmentation provides the basis for rust removal and exposure of subsequent base-metal.
That is, as a result of these micro-indentations, surfaces are cleaned and profiled simultaneously. Moreover, the appealed compressive residual stress in the workpiece is verifiable to a significant subsurface depth (Fig. 1). 1
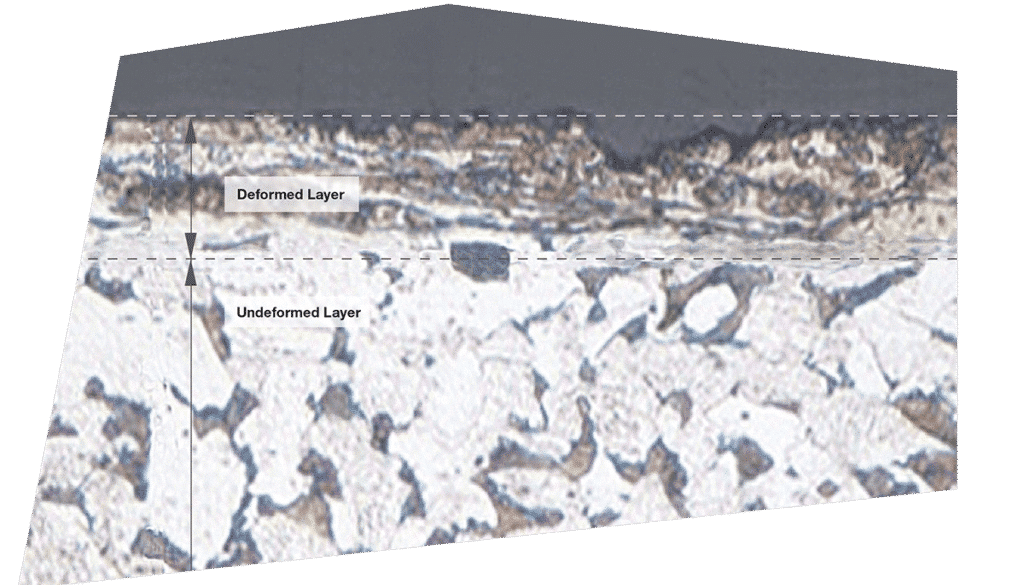
Figure 1: Cross sectional micrograph depicting worked layer and 100 µm undisturbed substrate of a Bristle Blasted surface (ABS-A steel) 2
Stango machined a common ship construction steel (ABS-A) by using the Bristle Blasting process and investigated thoroughly the developing longitudinal and transverse stress, respectively, via x-ray diffraction. Both follow a similar pattern and reach the greatest compressive residual stress within the vicinity of 30 – 50 μm.
Fig. 2 illustrates that compressive residual stress is measurable to a depth of ~300 μm before normalization. From this Stango infers an enhancement of component life, because of improved resistance to crack growth, as well as delaying the onset of stress corrosion cracking. 3
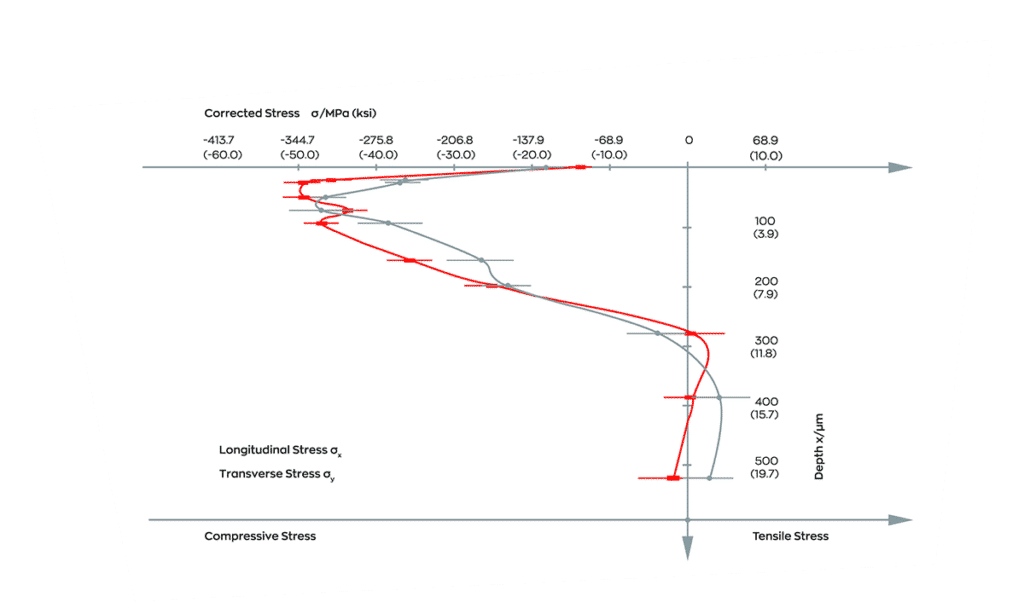
Figure 2: Residual stresses measured using x-ray diffraction for a Bristle Blasted surface (ABS-A steel) 2

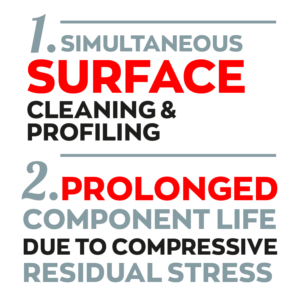
REFERENCES:
[1] Stango, R.J., “Compressive Residual Stress Generated by Bristle Blasting Process with Implication upon SCC”. In NACE Corrosion Conference 2014, San Antonio, Paper no. C2014-5152, Page 3. [2] Ibid., page 4. [3] Ibid., page 4.
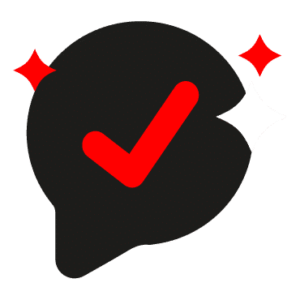
Download Dr. Prepper No. 5
You can also download the complete Dr. Prepper editions: