Dr. Prepper
Edition 11
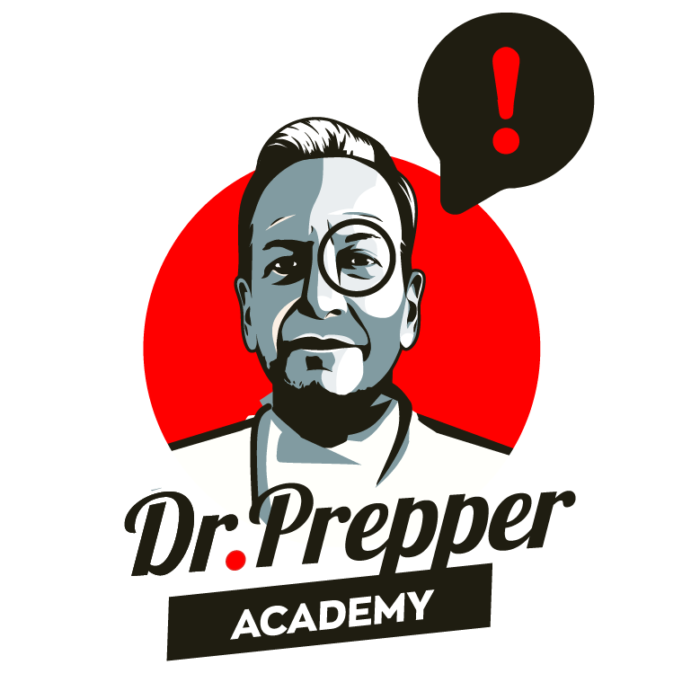
BRISTLE BLASTING IN THERMAL SPRAYING: ENHANCING COATING ADHESION
In the 11th edition of Dr. Prepper, we delve into a case study conducted by the University of Technology – Beijing, and the College of Materials Science and Engineering – Beijing, led by Yingying Ding, Hui Li, and Yingliang Tian. The study focuses on adhesive strength in thermally sprayed coatings, a critical factor for performance. It introduces Bristle Blasting as an innovative surface pretreatment and compares its effectiveness to grit blasting on mild steel and aluminum alloys.
Bristle Blasting proves to be a practical solution, particularly in situations where on-site grit blasting is challenging. Additionally, the study underscores the significance of considering substrate material, crucial for optimizing coating adhesion with Bristle Blasting as a surface preparation method.
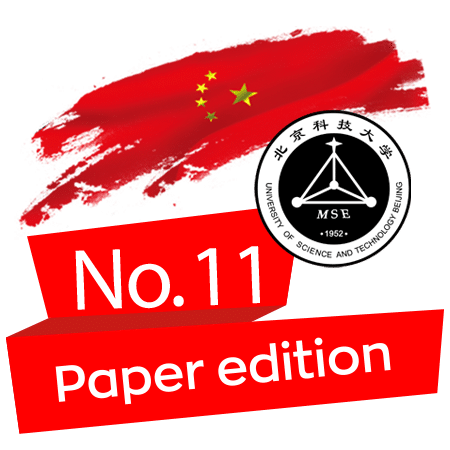
The regular RED PAPER from MontiPower®. Full of nice to know – and need to know – facts about the most optimal surface preparation since 1987.
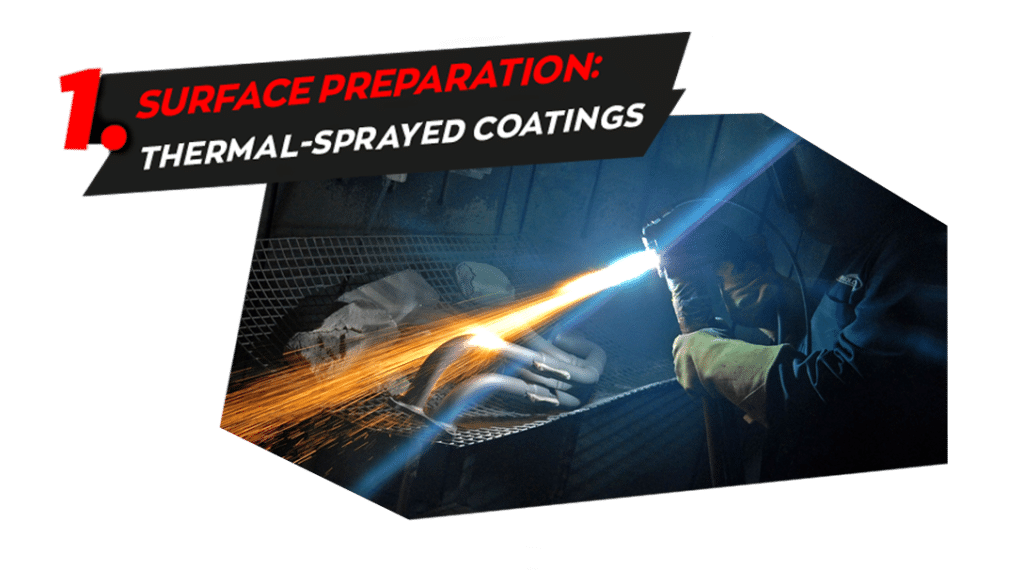
Thermal-sprayed coatings find extensive application across various industrial sectors for surface engineering solutions. Ensuring sufficient adhesive strength between the coating and substrate is imperative, constituting a fundamental service requirement. Typically, the substrate surface undergoes meticulous preparation before spraying to furnish a cleaned and roughened surface, facilitating adequate bonding for the deposited coating. This procedural step is essential and significantly influences the overall performance of the coating.
Soft substrate materials like aluminum alloys, copper, etc., face significant challenges due to the presence of embedded grit particles at the substrate/coating interface. Moreover, in certain on-site operations, employing traditional grit-blasting machines proves challenging, given their reliance on air compressors and substantial grit consumption. Additionally, environmental concerns arise from the noise and hazardous dust byproducts associated with such machines. A surface pre-treatment utilizing mobile facilities with straightforward operation proves more advantageous for these industrial applications.
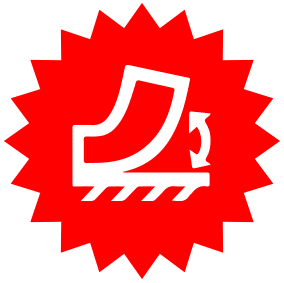
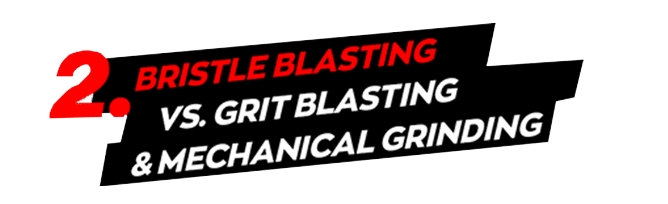
This study aims to assess the feasibility of using Bristle Blasting in thermal spraying, focusing on metallic (Ni5Al) and ceramic (Al2O3) coatings on substrates like mild steel (A283) and aluminum alloy (7075). The coatings will be applied on surfaces prepared by three methods: Bristle Blasting, grit blasting and mechanical grinding.
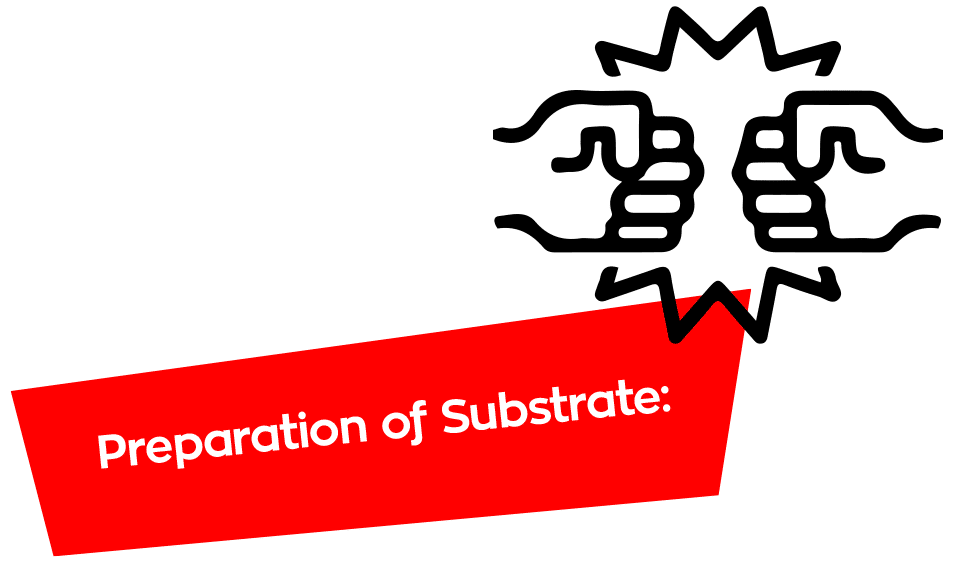
The primary aim was to compare grit blasting and Bristle Blasting as surface pretreatments, with mechanical grinding serving as a control group to assess the impact of surface roughness. In grit blasting, 20-mesh corundum particles (Pigeon Group) were employed with a blasting air pressure of 0.6 MPa and a blasting distance of 60 mm. Mechanical grinding involved manual use of 800# SiC sandpaper on an automatic grinding machine. Bristle Blasting utilized a commercial blaster (Monti SE-677-BMC) with a fixed wheel rotation speed of 2150 rpm, considering penetration depth as a key parameter.
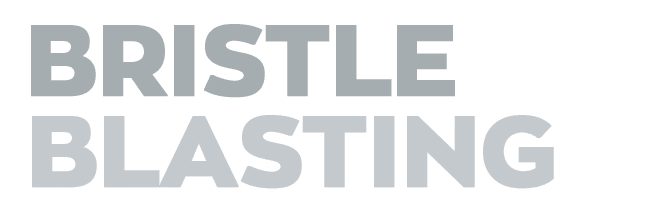
During operation, the rotating bristle tips strike the target surface with a kinetic energy similar to the impact of blasting grit. This process repeated continuously results in thousands of localized impacts, rebounds, and the formation of craters, thereby leaving a cleaned and roughened surface. The main advantage of this technology is its simplicity and ease of use. The Bristle Blaster® is half a meter long and several tens of centimeters high; It can be easily driven by a battery, electric, and pneumatic motor. It can be mounted on an automated positioner or handled manually so that the operation only needs a very small space, unlike grit blasting typically requiring a large soundproof booth or protection.
TEST: Some workers have tried to use Bristle Blasting as a surface pretreatment for painting and have shown that it was possible to generate a roughened surface, whose average roughness (Ra) was about 3.35µ.
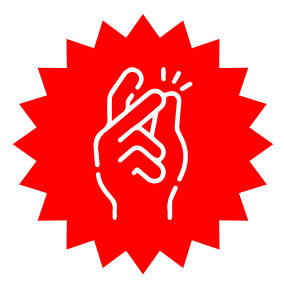
The main advantage of this technology is its simplicity and ease of use.
In recent years, Bristle Blasting has emerged as a new approach in surface preparation that has drawn attention from industry. This process is fundamentally a mechanical abrasion process using a rotating brush-like wheel. The wheel consists of many sharpened, high-strength steel wires whose tips are specially designed with a forward-angle bend, i.e., the shank of the wire is bent in the direction of rotation (fig. 1). During operation, the rotating bristle tips strike the target surface with a kinetic energy similar to the impact of blasting grit. This process repeated continuously results in thousands of localized impacts, rebounds, and the formation of craters, thereby leaving a cleaned and roughened surface.
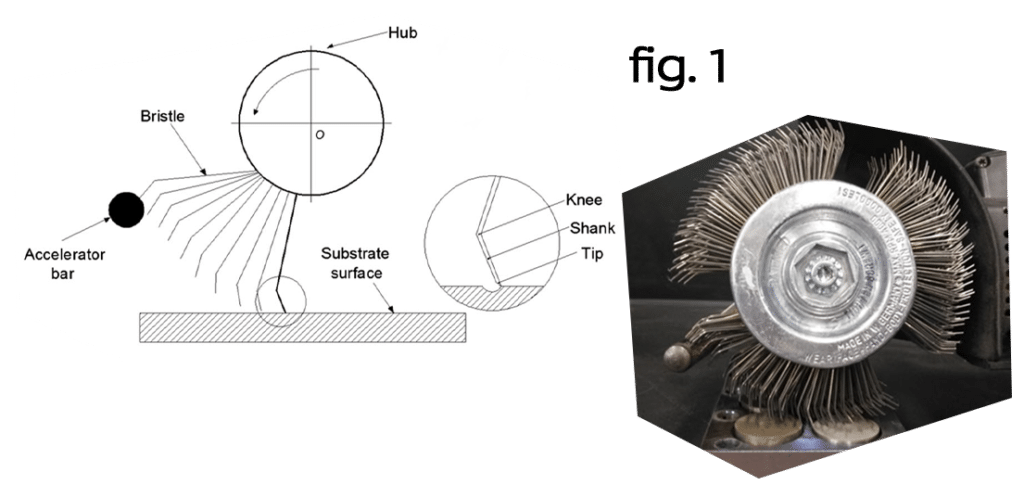
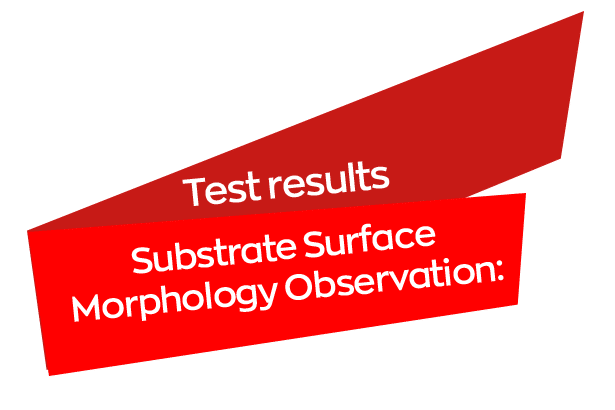
The LEXT OLS4100 confocal laser scanning microscope was used to characterize surface topography with enhanced optical resolution. This method provides a balanced combination of high test accuracy and speed, evaluating both 3D and 2D surface morphology.
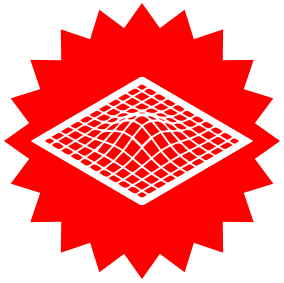
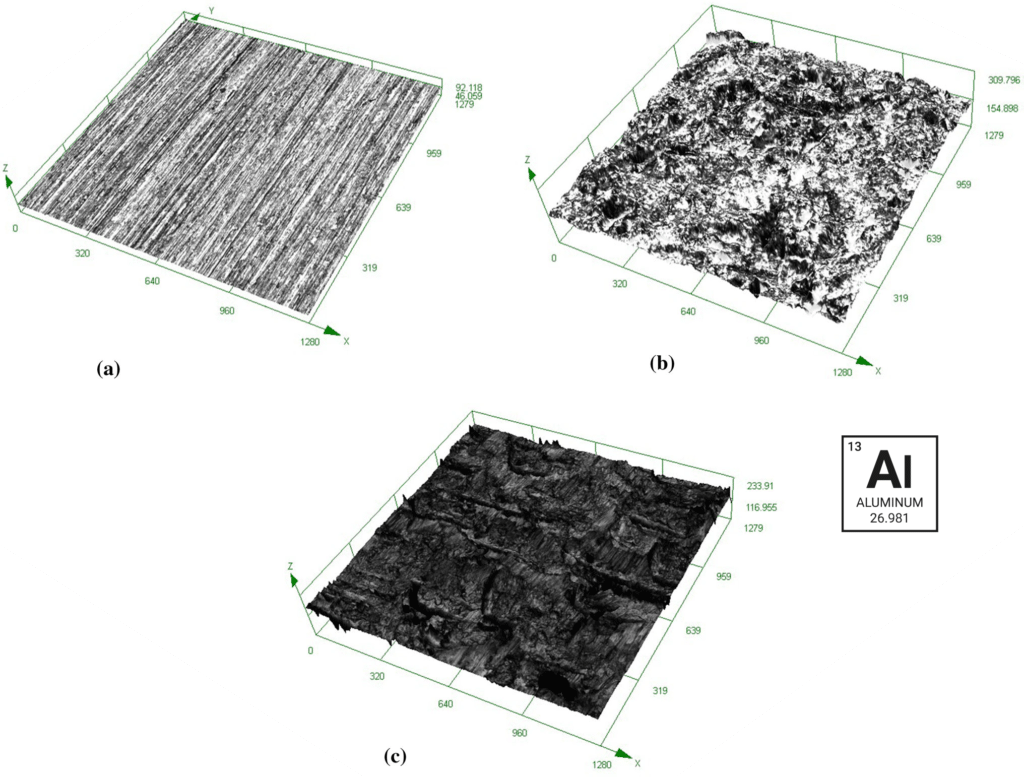
The surface morphology of the steel
substrate treated by different methods:
(a) Grinding
(b) Grit blasting
(c) Bristle Blasting (3 mm)
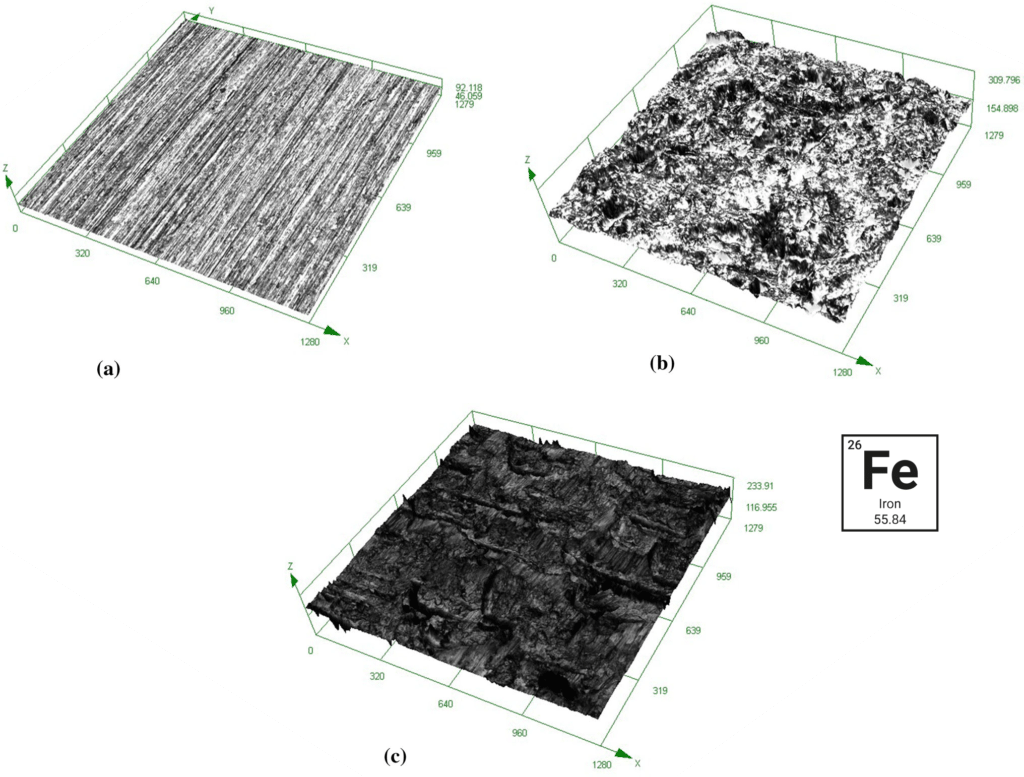
The surface morphology of the steel
substrate treated by different methods:
(a) Grinding
(b) Grit blasting
(c) Bristle Blasting (2 mm)
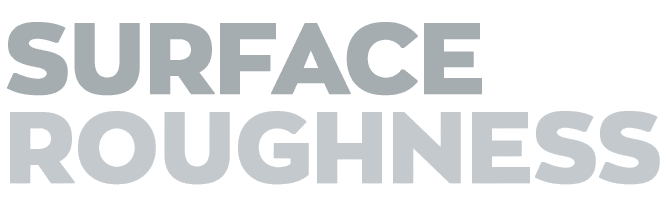
In the case of the 7075, the surface average roughness Ra increased abruptly from 0.834 ± 0.185 to 2.450 ± 0.606 μ when the penetration depth changed from 1 to 2 mm, implying that more substrate materials were chipped out. However, there was no distinct difference between the samples treated with apenetration depth of 2 and 3 mm in terms of average roughness (Ra) and profile slope (Rdq). This is presumably due to the plastic deformation of the 7075 substrate when the bristles continuously impacted on the substrate, as observed in fig.2. As the penetration depth increased, there was a tendency for a gradually decrease of the surface skewness (Rsk), indicating that the profile asperities were shallow and depressed. For the A283, when the penetration depth increased, the roughness increased linearly, as shown in fig. 2.
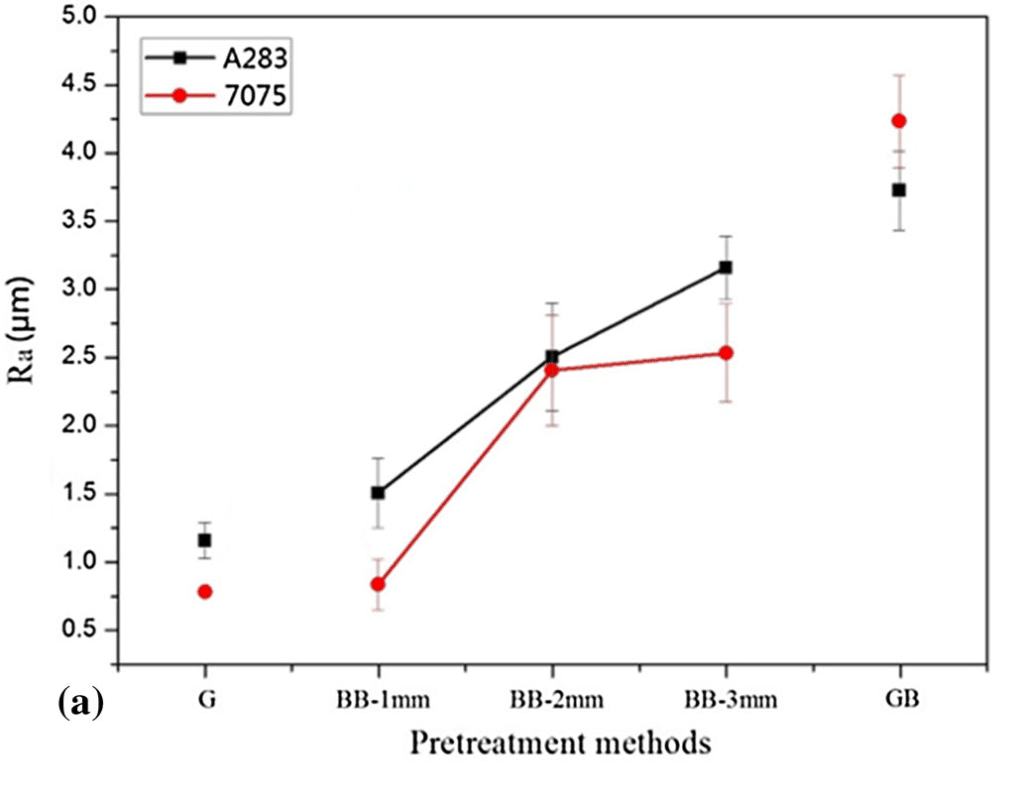
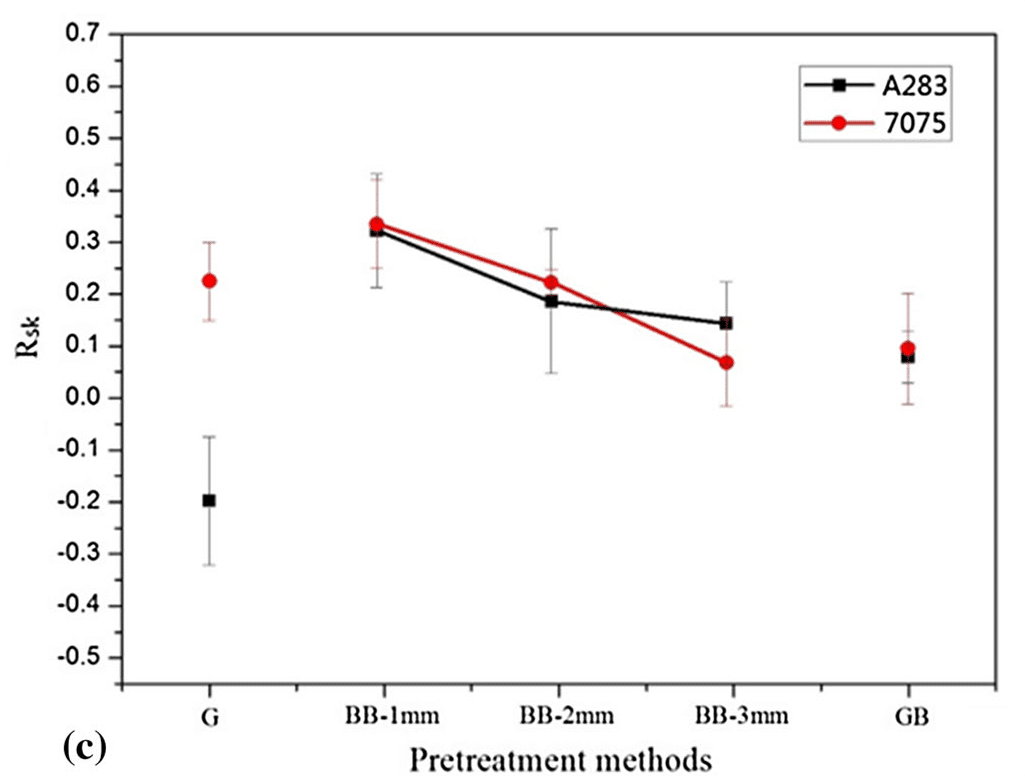
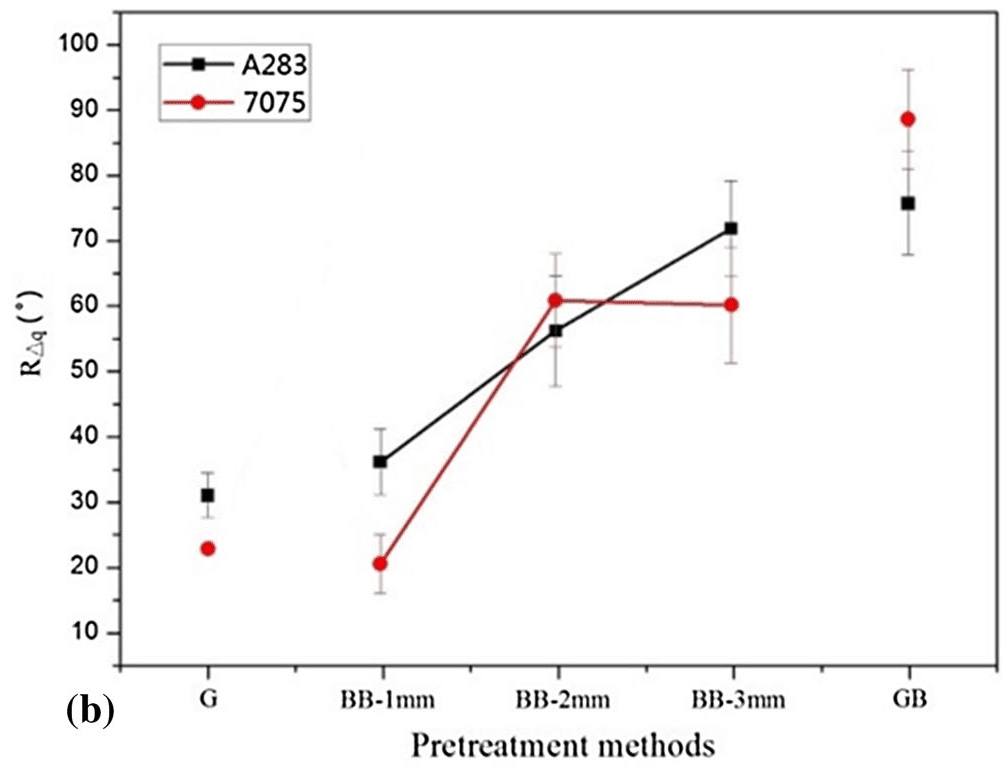
fig. 2
Surface roughness of substrate with different treatment. (a) Ra, (b) Rdq, (c) Rsk; G grinding, GB grit blasting, BB Bristle Blasting.

The study compared bristle-blasted and grit-blasted surfaces. Although bristle-blasted surfaces appeared visually brighter, they were less rough than grit-blasted ones. For 7075, an increase in penetration depth from 1 to 2 mm led to a significant rise in average roughness (Ra), indicating more substrate material chipping. Plastic deformation occurred at deeper depths. For A283, increasing penetration linearly increased roughness. A283 reached grit-blasted roughness at 3 mm, limited by insufficient kinetic energy. Despite similar Ra values, bristle-blasted surfaces were less uniform due to bristle wires’ spacing, resulting in larger peaks and valleys compared to grit-blasted surfaces fig. 3.
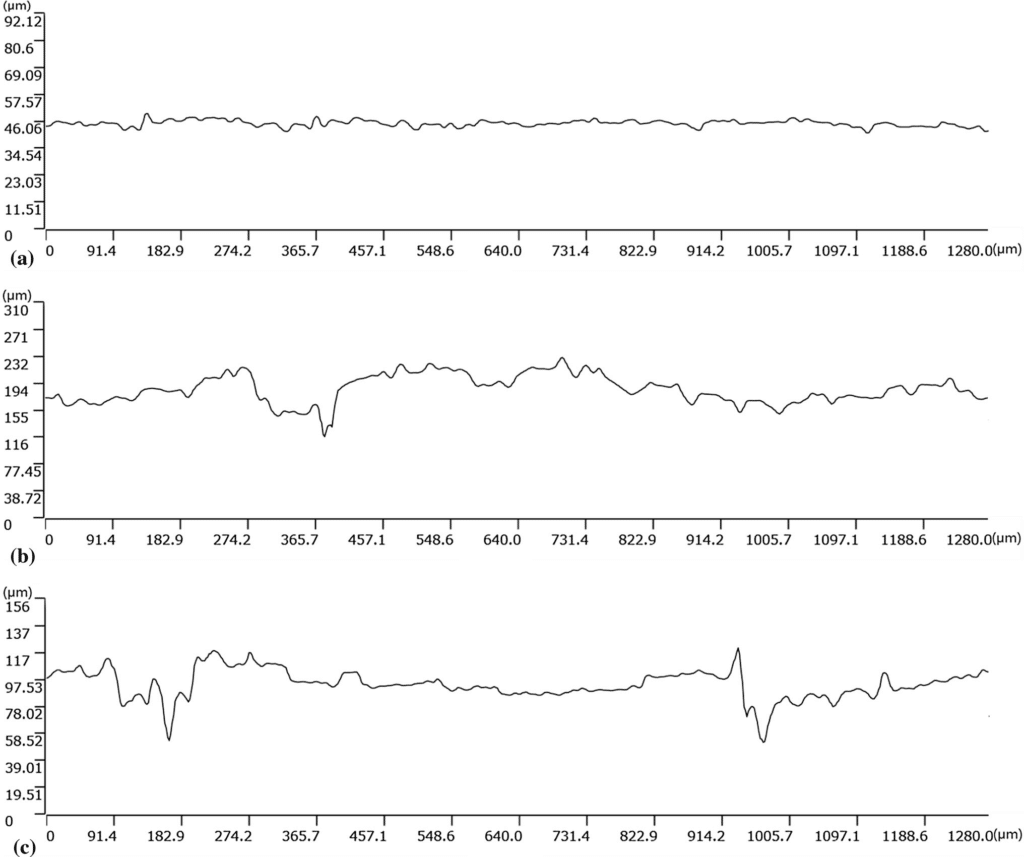
fig. 3
2D profile of the steel substrate surface (A283) with different treatments: (a) as-ground, (b) as grit blasted, (c) as bristle blasted with 3 mm penetration.
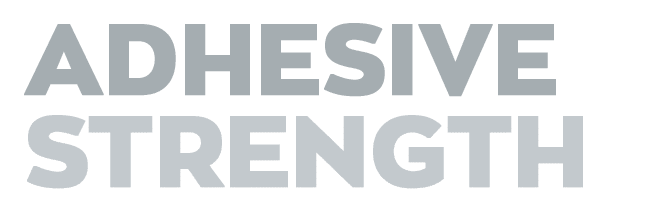
The main drawback of using grit-blasting for surface preparation is the presence of grit residues at the interface, especially problematic for soft materials. While subsequent ultrasonic cleaning can remove these residues, its on-site application is challenging. This issue is entirely avoided when employing Bristle Blasting for surface preparation. The most appealing aspect of Bristle Blasting lies in its simplicity and cost-effectiveness, particularly for on-site operations.
Unlike grit blasting, where collecting and recycling massive rebounded abrasive particles in open spaces is difficult, Bristle Blasting offers flexibility and processing efficiency comparable to standard grit blasting and mechanical roughening. Based on laboratory experience, the processing speed during Bristle Blasting can reach about 1 square meter of surface in 1 hour, significantly faster than laser texture processing.
In Bristle Blasting, surface abrasion occurs through the extensive excavation of the metal surface by the bristle tips, resulting in numerous localized shoveled craters..
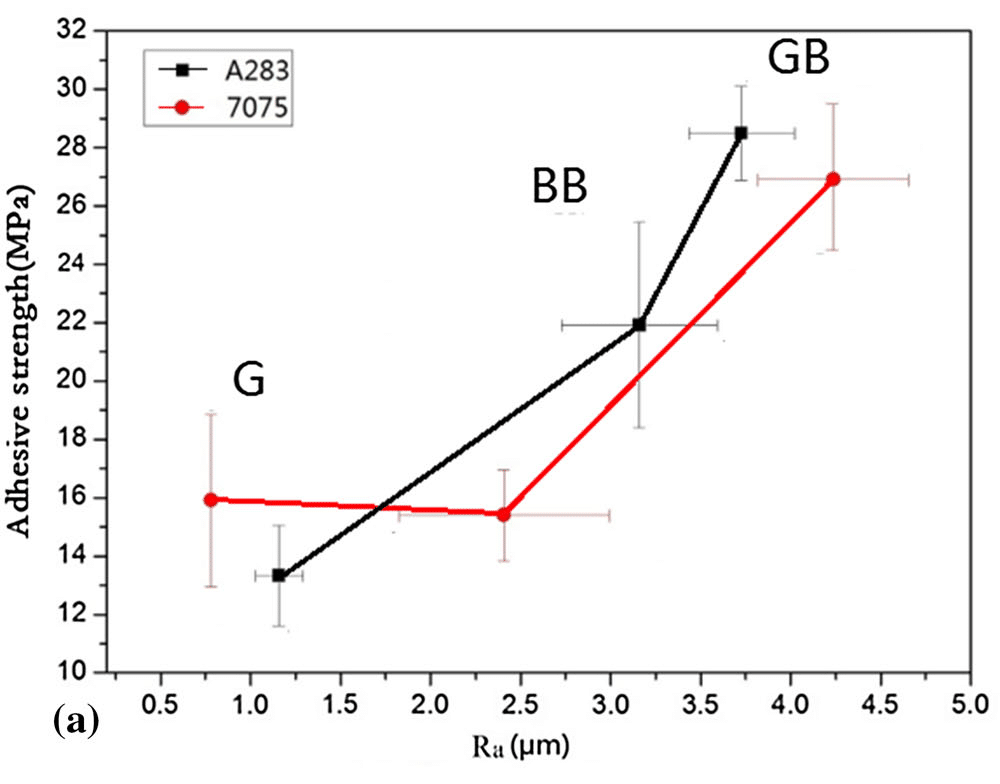
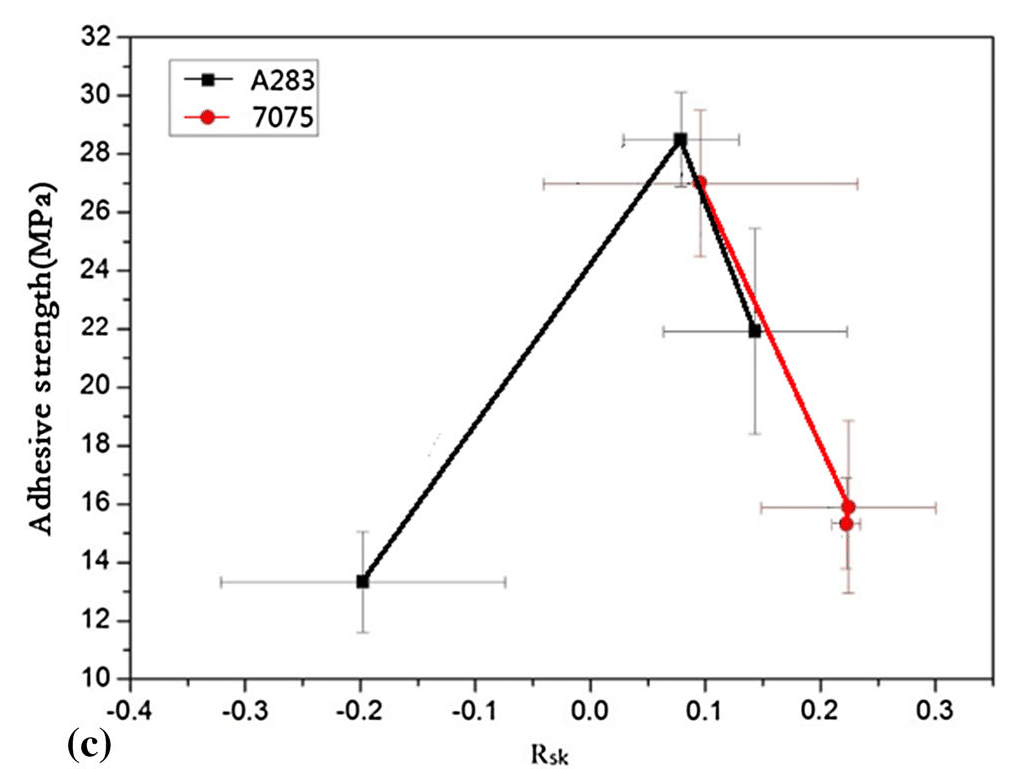
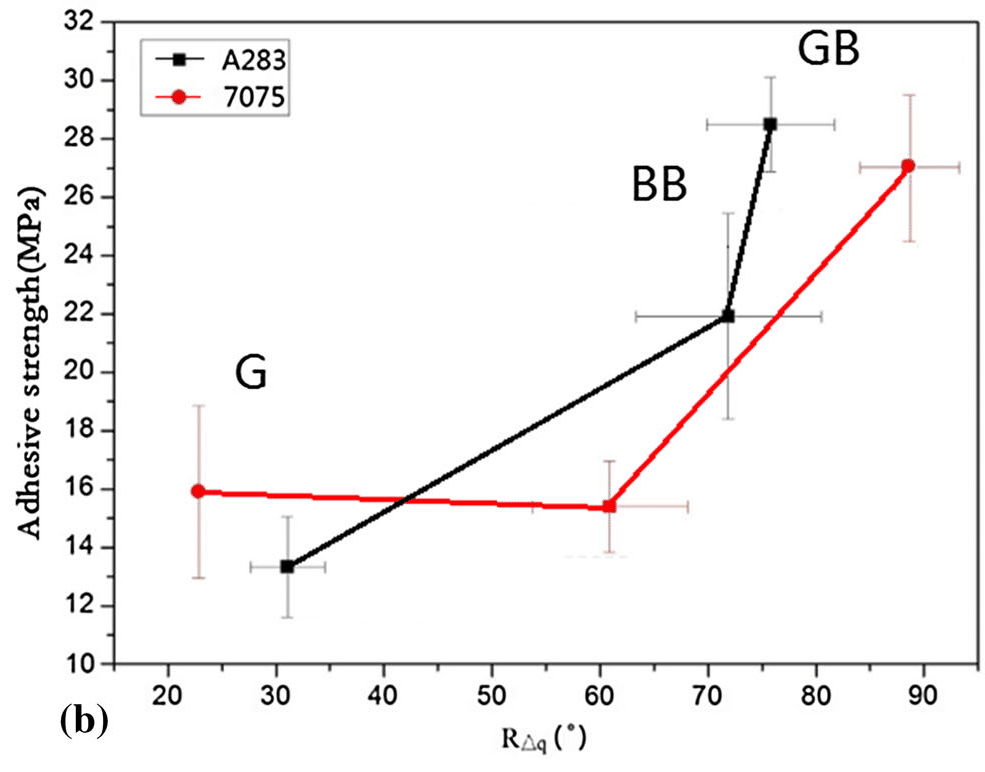
fig. 4
Dependence of the Ni5Al coating adhesion upon different surface roughness parameters: (A) Ra, (b) Rdq, (c) Rsk
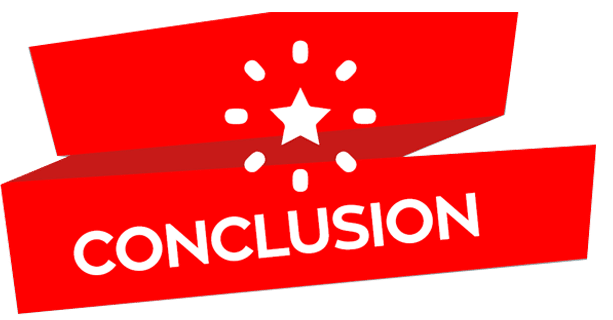
This study investigated the feasibility of applying Bristle Blasting in relation to thermal sprayed coatings. The main preliminary results are as follows:
The adhesive strength of thermally sprayed coatings on substrates subjected to different pre-treatment methods showed a gradual increase from grinding, Bristle Blasting to grit blasting. In the case of the Ni5Al coating, the surface preparation with Bristle Blasting yielded approximately 60% of the adhesive strength compared to the grit blasting method.
Bristle Blasting appears to be a promising solution for steel and aluminum alloy substrates when grit blasting is not applicable. However, it is essential to consider the substrate material in the selection of blasting parameters.
WE BELIEVE IN THE POWER OF INNOVATION
By preparing optimal surfaces, we make coatings work better. Montipower® has been innovating original surface preparation machinery, quality made in Germany, since 1987.