Grit blasting
Surface preparation without grit blasting with MontiPower’s power tools
Certain standards apply to the surface preparation of steel. Normally, the use of industrial coatings requires a surface cleanliness of Sa 2.5 (or SSPC-SP10 or NACE 2) and a specific roughness based on the surface preparation standards. In most cases, abrasive grit blasting is used for this purpose. ‘Sand blasting’ has traditionally been the best known method of grit blasting, but nowadays, grit blasting can also be done with other materials. But how does surface preparation with grit blasting actually work? What types of grit blasting are there, what are the advantages and disadvantages, and how are MontiPower’s power tools a good alternative for this?
What is grit blasting?
Grit blasting is usually done for the surface preparation of steel and other substrates. In this way, the surface is stripped of coatings, paint, rust and other dirt. For the surface preparation with grit blasting, two elements are needed: an abrasive media (grit) and air. By blasting the grit under high pressure onto the surface, the coating will be removed from the surface – due to the abrasive effect this creates. In addition to removing the coating, paint, millscale, rust or other dirt, the high impact of the grit also creates a structure on the surface. This creates the ideal adhesive layer for a new coating.
Types of grit blasting
Grit blasting is possible in many ways. Traditionally, sandblasting has been the best known and most widely used form of grit blasting. Here, sand grains are added as an abrasive media to prepare the surface. Over the years, more and more ways of sandblasting have been developed, such as bead blasting, wheel blasting, vapor blasting and vacuum blasting. A distinction can be made between dry grit blasting and wet grit blasting. Examples of dry grit blasting are, in addition to blasting with sand, grit blasting with glass and with corundum (aluminum oxide). In contrast, grit blasting can also be done with water. This so-called wet grid blasting is mostly used to prepare surfaces of delicate materials. In contrast to grit blasting with sand or other dry materials, this is done under low pressure. As a result, the abrasive media is gradually distributed over the entire surface, so that even the more fragile surfaces can be prepared and cleaned. However, due to the low force with which this is done, grit blasting with water is not suitable for creating a new bonding layer.
What are the disadvantages of grit blasting?
Although grit blasting has been done for many years and more and more new ways of grit blasting have been developed, grit blasting also has its disadvantages. The methods generally used for this purpose are not suitable in every situation. Grit blasting generally has a very persistent effect on the surface, which can quickly and easily damage objects. Partly because of this and the fact that grit blasting requires a lot of preparation, it is recommended that this is always carried out by a professional. But this is not the only disadvantage. Sandblasting in particular not only has a severe effect on the surface, but also on the health of people and animals. Because of the great force with which the sand hits the surface, the grains of sand break up into small particles. Inhaling these particles can be very harmful. It is the reason why it is forbidden to sandblast in many countries.
Also, the traditional ways of grit blasting, especially when cleaning and preparing smaller surfaces, are relatively expensive. The blasting of such surfaces is a large investment in terms of time and money, due to the high preparation costs, such as the transportation of the equipment and the possible removal of the surface.
Alternative for the grit blasting machine: the Bristle Blaster®
The Bristle Blaster® is MontiPower’s alternative to grit blasting. The grit-free patented Bristle Blaster® is able to produce a surface quality comparable to grit blasting both in cleaning of the object and in roughness capacity:
– surface cleanliness of Sa 2.5 or SSPC-SP 10
– roughness capacity up to 120 μm Rz (ca. average 65-83 μm Rz on API 5L steel)
The major advantages of the power tools over traditional blasting methods are their simplicity in use and their relatively low cost. This is because the surface is prepared with a light, handheld machine. Other alternatives to grit blasting that are used to work smaller areas are also unable to prepare a surface profile suitable for industrial coating. In addition, these other alternatives to grit blasting usually cannot meet the surface cleanliness and roughness requirements, which is possible with the Bristle Blaster®.
Bristle Blasting is ideally suited for portable usage as no protective suits with closed system respiratory equipment are required and no complex machinery or other grit media recovery equipment is needed. Only the application of standard personal protective equipment (PPE) is recommended for the eyes, face, hands and respiratory. Apart from the materials removed, no other additional or environmentally harmful waste products are produced.
How do the alternative grit blasting tools work?
MontiPower’s alternative grit blasting tools are manually operated tools equipped with a rotating brush. Due to the specially designed curved brush tips, the surface is cleaned quickly and easily, with similar results to traditional grit blasting. Because the tips are released with a great deal of force from behind the tools’ accelerator bar, they immediately retract from the surface, providing the same roughness as with grit blasting. In this way, the Bristle Blaster® offers all the advantages of grit blasting, including the high-quality result. This makes MontiPower power tools for many markets the relatively cheap, easy to operate and effective alternative to the traditional grit blasting machine.
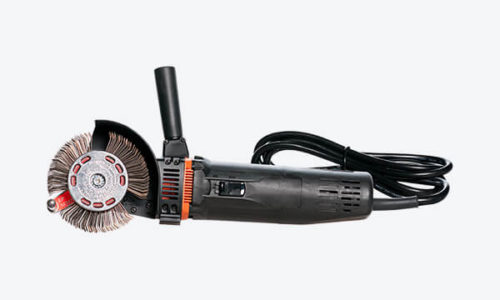
