Dr. Prepper
edition 7
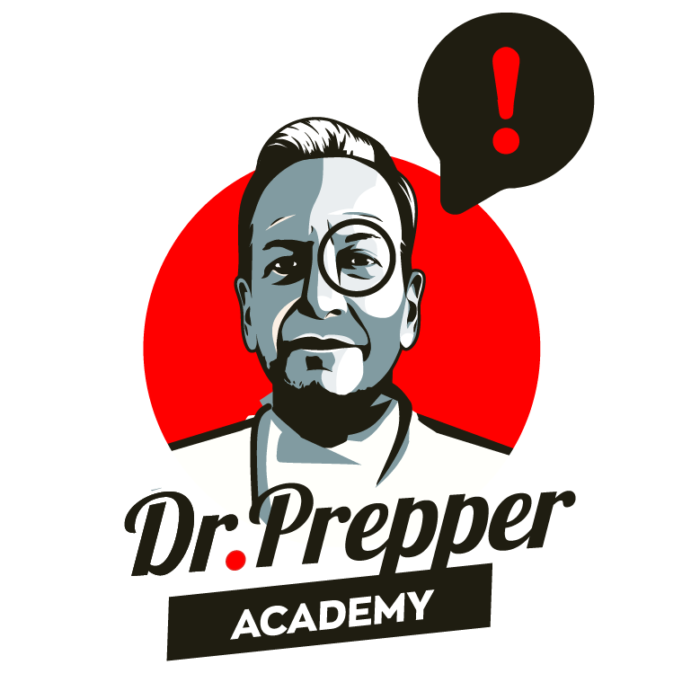
Coating Longevity by Proper Surface Preparation
This seventh edition of Dr. Prepper takes us back to the basics of why proper surface preparation is so important, and how the Bristle Blaster® manages to live up to such expectations. Poor surface preparation and coating application can lead to premature coating degradation, particularly loss of adhesion, and a greater risk of corrosion. There have been appropriate, well-defined standards available for many years, but these are not always applied, or not correctly. So, what should you take into account in your surface preparation in future?
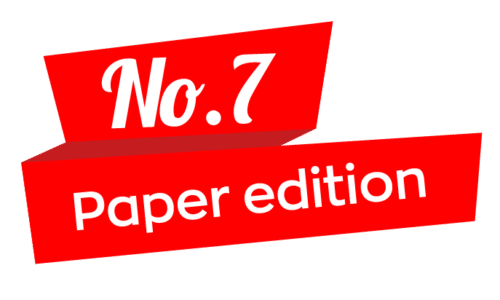
The regular RED PAPER from MontiPower®. Full of nice to know – and need to know – facts about the most optimal surface preparation since 1987.
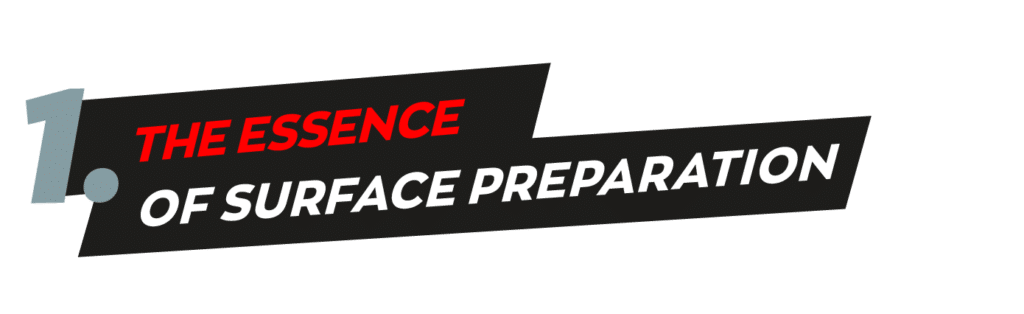
Proper preparation of the steel surface before applying an external coating is the core of any corrosion control programme. Any compromises in surface preparation will generally compromise the coating’s field performance as well, regardless of its technical quality.
Surface preparation refers to the cleaning and/or pre-treatment of metal and adjacent coating surfaces in order to ensure an optimal bond between the surface to be coated and the coating to be applied.
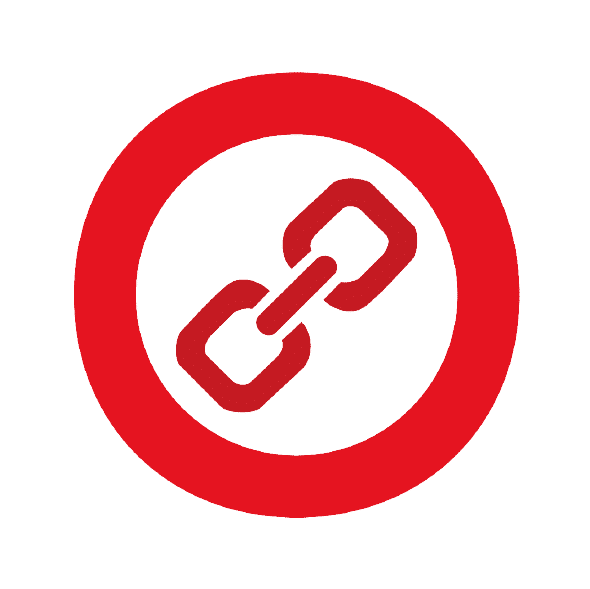
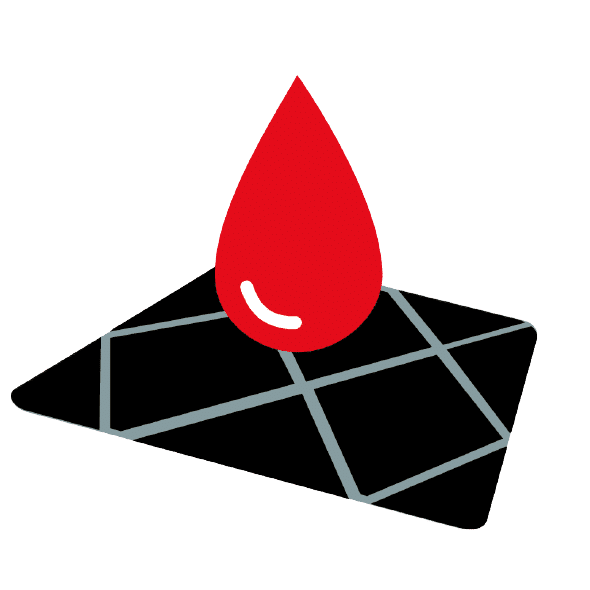
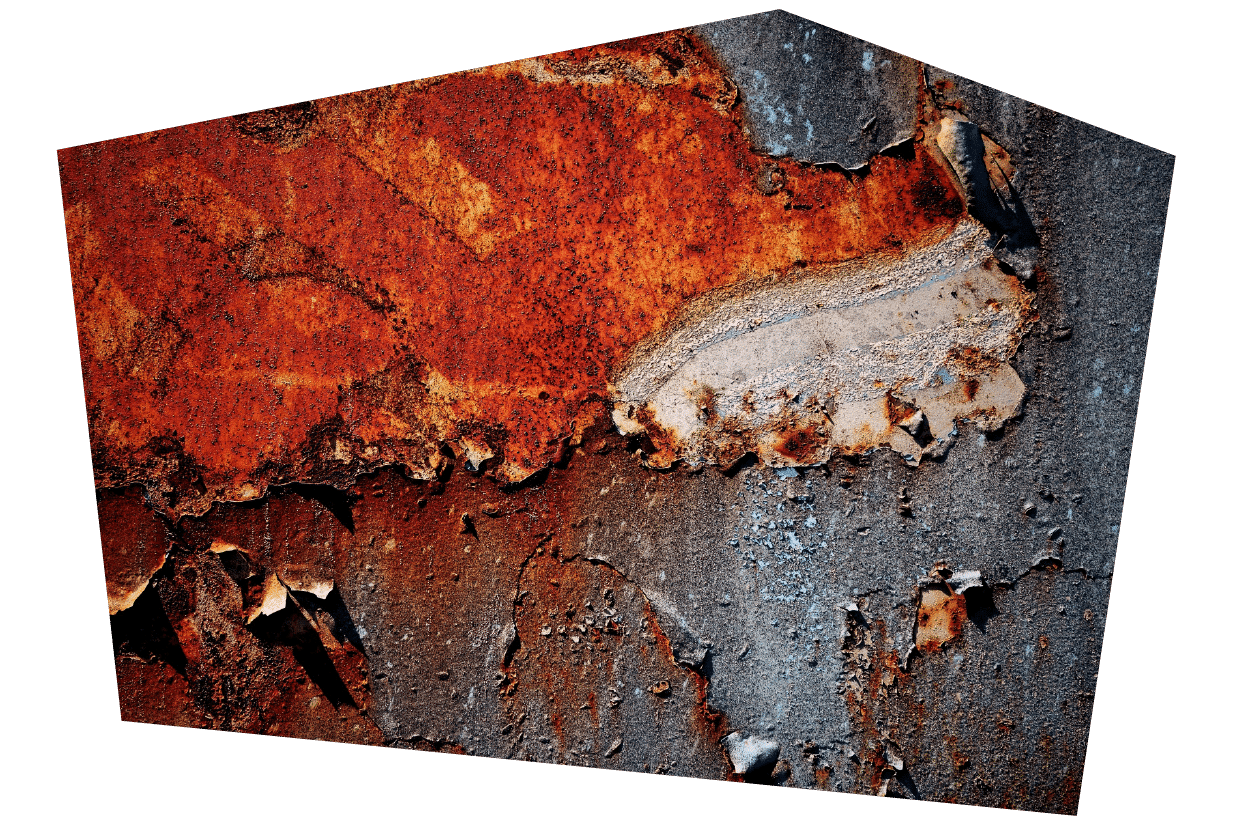
Coating degradation issues that create corrosion risks within a steel structure’s design life will have one of the following causes:
• Inappropriate coating material and/or coating process
• Poor surface preparation and/or application
• Interaction with operating environment
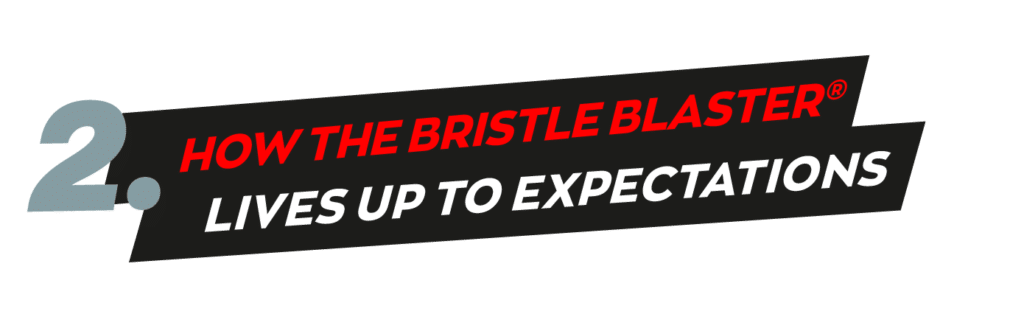
10,000 strikes per second per 23 mm belt, without heating the surface The Bristle Blaster®’s core feature is its accelerator bar. This suspends and accelerates individual bristles as they rotate, increasing the kinetic energy with which the tips impact the surface. This system combines an abrasive blasted finish with the high mobility and flexibility of a portable hand-held tool.
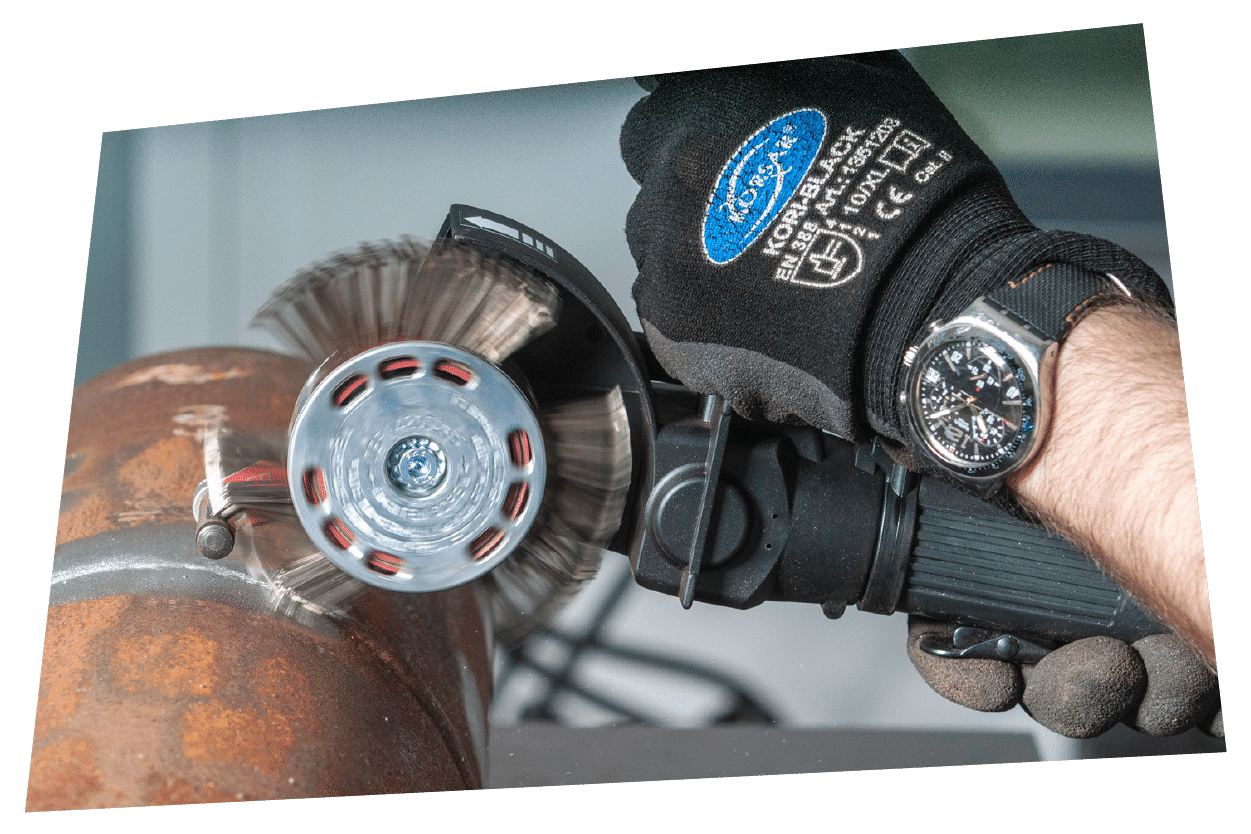
The processes used before and after Bristle Blasting are similar to loose abrasive blasting. Operators should wear safety glasses. It is possible to check the degree of cleanliness visually during blasting. The bristles are suitable for reclamation and it is possible to connect a dust extractor. Compressed air used for preumatic Bristle Blasting must be free of oil or condensation.
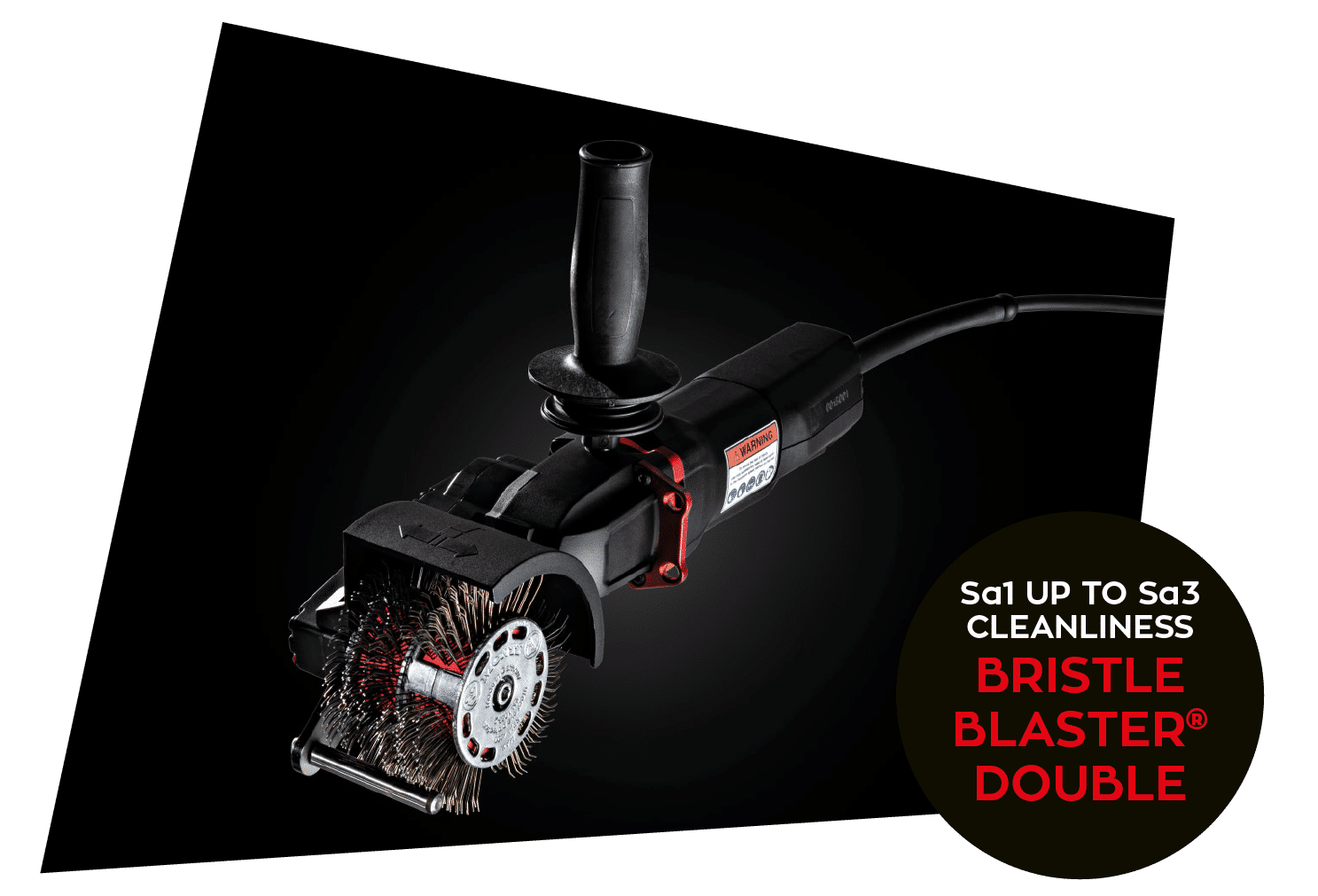
Depending on the brush and type, Bristle Blasting meets power tool cleaning requirements and the current normative cleanliness standard of Sa1 up to Sa3 for loose abrasive blasting. For production, a general rule of thumb is that 1 operator can prepare 1 m² in 1 hour using 1 Bristle Blaster® of 23 mm in width. With Bristle Blaster® Double, 1 operator may achieve 3 m² of surface preparation per hour. Prepper Q4 and Prepper Q10 are also available in wider configurations. Subsea Bristle Blasting makes use of water hydraulics.
With Bristle Blaster® Double, 1 operator may achieve 3 m² of surface preparation per hour. Prepper Q4 and Prepper Q10 are also available in wider configurations. Subsea Bristle Blasting makes use of water hydraulics.
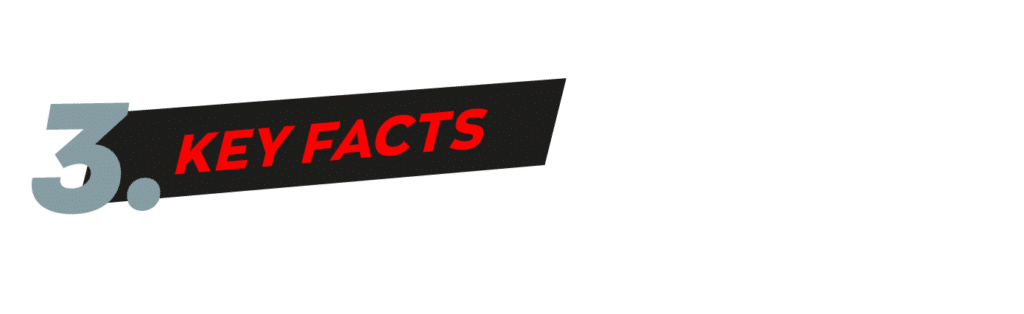
• Sa3 is approximately equivalent to NACE No.1/SSPC-SP5
(White metal blast cleaning)
• Sa2½ is approximately equivalent to NACE No.2/SSPC-SP10 (Near-white metal blast cleaning)
• Sa2 is approximately equivalent to NACE No.3/SSPC-SP6
(Commercial blast cleaning)
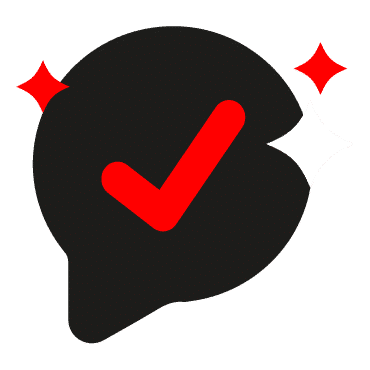
Download Dr. Prepper No. 7
You can also download the complete Dr.Prepper edition: